The relationship between drop size distribution and extinguishing capacity of a water mist is not straight-forward. As a general guideline however, very fine particles enhance heat absorption and generation of water vapor, since as the droplet diameter decreases, the droplet reaction surface per liter of water increases significantly.
By definition, water mist is a water spray for which the 99% of the total volume of liquid (Dv0.99) is in droplets of diameter smaller than 1000 microns at the minimum design operating pressure of the water mist nozzle.
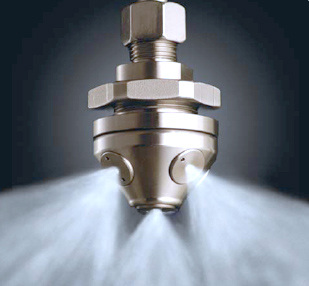
Major uses water mist spray
Properly designed water mist spray systems can be effective on both liquid fuel (Class B) and solid fuel (Class A) fires. Experiments have shown that that droplets smaller than 400 microns are effective for extinguishment of Class B fires, whereas larger droplet sizes are effective for Class A combustibles.
Categories of water mist systems
Water mist systems generally fall in three (3) categories:
- low pressure systems: the distribution piping is subject to pressures of 12.1 bar (175 psi) or less.
- intermediate pressure systems: the distribution piping is subject to pressures ranging between 12.1 bar (175 psi) and 34.5 bar (500 psi).
- high pressure systems: the distribution piping is subject to pressures of 34.5bar (500 psi) or greater.
Similar to other systems, dry-pipe water mist systems, wet-pipe water mist systems, deluge water mist systems as well as preaction-type water mist systems are available.
Limitations of water mist spray systems
Water-mist spray systems shall not be used for protecting materials, which when in contact with water, either react violently or produce hazardous byproducts. Materials for which the use of water-mist systems must be avoided are the following:
- reactive metals such as lithium, sodium, potassium etc.
- metal amides and alcoxides.
- carbides, halides, hydrides, oxyhalides.
- silanes, sulfides, cyanates.
- liquified gases at cryogenic temperatures like liquified natural gas.
Components of water mist systems
The use of either seamless copper tubes or stainless tubes is allowed for low pressure systems. For low pressure systems, use of screwed (threaded) fittings shall be limited only to pipe sizes smaller or equal to 2 inches.
For intermediate and high pressure systems, all piping will have to be in accordance with ASME B31.1 Power Piping Code. Screwed connections shall comply with ANSI B1.20.1
A test connection shall be provided at the most hydraulically remote point on the water mist system.
For more information for other system components like hangers, valves, strainers, nozzles, pumps, instruments, detection, actuation (unless manual-only actuation is allowed by the Authority Having Jurisdiction, only automatic actuation has to be used) , alarm and control systems etc, user is kindly requested to consult NFPA 750 in more detail.
Water mist system design
Every water mist system shall have at least one automatic water supply. A minimum 30 minutes duration of discharge needs to be taken into consideration, unless other more strict requirements need to be fulfilled.
An extra supply (reserve supply ) of extinguishing agent (including additives andatomizing medium, if used) connected to feed into the automatic system should be considered for all installations. The reserve supply is normally actuated either manually, electrically or pneumatically.
Water mist system testing
Hydrostatic tests
For low pressure systems, hydrotests will have to be carried out as follows:
- for system working pressure less or equal to 10.4 bar (150 psi), all system piping and interconnected appurtenance shall be subject to a hydrostatic test of 13.8 bar (200 psi) for 2 hours
- parts of systems or systems subject to working pressures over 10.4 bar (150 psi) shall be tested at a pressure of 3.5 bar (50 psi) over the working pressure.
Intermediate as well as high pressure systems shall be hydrostatically tested to 1.5 times the working pressure for 10 minutes, followed by 110 minutes at the working pressure without pressure loss in compliance with the ASME B31.1 code.
Air tests
For dry and preaction systems, an air pressure leakage test at 2.8 bar (40 psi) shall be held for 24 hours besides the standard hydrostatic test.Any leakage leading to a pressure loss in excess of 0.1 bar (1.5 psi) during the 24 hours period shall be rectified.