An eccentric reducer is a type of pipe fitting used to connect pipes of different sizes. They are called "eccentric" because they are not symmetrical, with one side having a larger diameter than the other. In pump suction piping, eccentric reducers can be used to connect pipes of different sizes while maintaining the required fluid flow.
Table of content:
Why to use eccentric reducers in pump suction piping?
Using eccentric reducers for centrifugal pump suction piping
Orientation of eccentric reducers
Straight length requirement for pump suction piping
Pump suction piping guidelines
When to use concentric and eccentric reducers
Why to use eccentric reducers in pump suction piping?
Normally the pump nozzles are smaller than inlet/outlet piping. That is why we need to use reducers and expanders at the pump suction and discharge piping. We have a choice of using concentric or eccentric reducers.
By using an eccentric reducer, the incoming fluid is redirected and its flow direction is changed. This change in flow direction helps to prevent the buildup of air or vapor pockets at the high point of the pipe, which can cause cavitation and damage to the pump.
Using eccentric reducers for centrifugal pump suction piping
Eccentric reducers are typically installed at the centrifugal process pump suction nozzles in order to facilitate proper transition from the the larger diameter (low flow velocity, moderate friction loss) suction piping to the pump suction nozzle.
You must ensure proper installation of eccentric reducer in pump suction piping to minimize accumulation of any air or gas bubbles in the suction. If concentric reducers are used, their upper part can allow accumulation of trace amounts of air or vapors at the pump suction. This can lead to creation of bigger gas bubbles near the pump suction.
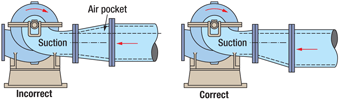
If these gas bubbles manage to escape from the reducer and get into the pump suction, resulting cavitation is damaging for the pump. Otherwise, if they stay trapped in the reducer, they reduce the available cross sectional area of the pipe for liquid flow. This results in higher liquid velocity in the pump suction, increasing frictional losses. It also affects the overall performance and long term reliability of the pump.
Orientation of eccentric reducers
When the source of supply is above the pump, then the eccentric reducers must be placed with the flat side at the bottom. Schematic given below shows eccentric reducers installation when source of supply is below or above the pump suction nozzle.
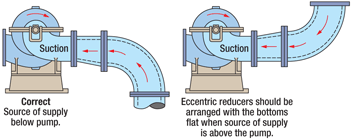
In case of long horizontal pipe runs, air pockets are avoided by installing the eccentric reducer with the flat side up.
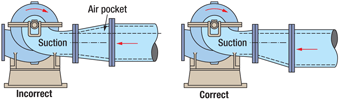
The above schematic shows eccentric reducers installation in case of long horizontal pipe runs.
Straight length requirement for pump suction piping
Pumps, especially centrifugal pumps, work best with a smooth, laminar flow. Higher liquid velocities and higher turbulence in the pump suction can sometimes cause cavitation in the pump. However you can minimize this by installing a sufficient length of straight run pipe before the pump suction.
ANSI/HI 9.8 American National Standard for Pump Intake Design (P21, 1998) states, “There shall be no flow disturbing fittings (such as partially open valves, tees, short radius elbows, etc.) closer than five suction pipe diameters from the pump. Fully open, non-flow disturbing valves, vaned elbows and reducers are not considered flow disturbing fittings.” This ensures stable and uniform flow onto the impeller eye, reducing pump failures due to flow-induced turbulence. This result in fewer pump failures over the life of the pump due to vibration caused by flow induced turbulence. In cases where several improperly specified parameters are present, it may be necessary to install straight piping next to the reducer inlet flange.
Whenever a low point exists at the pump's suction line and a concentric reducer is used at pump suction nozzle, it is possible to have vapor accumulation close to the pump suction nozzle (Picture-2). In such cases, straight horizontal pipe between reducer and pump suction should be kept to a minimum. In such installations, the reducer flange is often directly connected at the pump's suction nozzle. There is no straight length of piping between the reducer outlet and the pump nozzle.
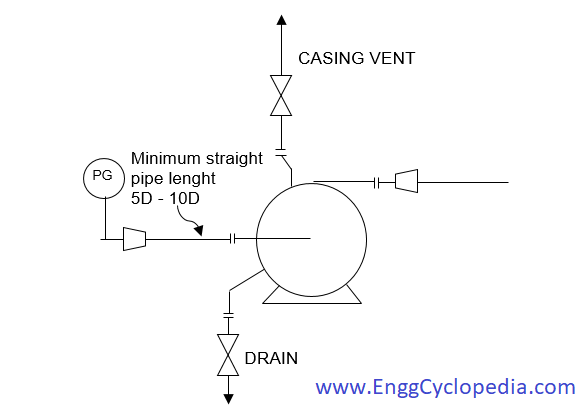
Straight pipe lengths are however connected to the inlet flange of an eccentric reducer.
Usually, a length equivalent to 5 times the pipe size is considered appropriate for the suction piping of a centrifugal pump. In some cases it may even be considered to install 5D length of a straight pipe run in pump suction next to the reducer flange.
In general it is acceptable to have a straight length of 5D to 10D between the pump suction and reducer, where D is the pipe size.
Sometimes due to space constraints, it’s just not possible to make provision for a sufficient settling distance in the pipework before the pump. In these cases, use an inline flow conditioner or straightener.
Pump suction piping guidelines
To ensure efficient pump operation and prevent damage, the following guidelines should be followed:
- To prevent the creation of a vortex that can draw in air or other vapors through the pumping system, the feed pipe must be completely submerged in the tank or vessel.
- To avoid drawing up solids or sludge, the feed pipe should not be placed too close to the bottom of the tank or vessel. Using a strainer in the pump suction piping can help address this issue, but it could lead to cavitation and friction loss by creating a significant pressure drop.
- To avoid putting a strain on the pump housing, it's important to independently support all piping, valves, and fittings. Furthermore, the forces and moments imposed on the pump nozzles must not exceed the allowable values specified by the vendor.
- Before tightening the bolts, it's crucial to accurately align the pipe connecting to the pump's inlet flange.
- To reduce pressure drop in the system, it's best to position the pump as near as possible to the suction source.
- To prevent any pockets in the line, the suction pipe must be routed in such a way that the suction nozzle elevation is below the vessel or tank nozzle elevation.
- A minimum space of 1 meter should be provided between pumps and any potential obstructions, such as large block valves, steam turbine piping, and tee-type support from grade.
When to use concentric and eccentric reducers?
Concentric and eccentric reducers are both types of pipe fittings that are used to connect pipes of different sizes. The choice between using a concentric or eccentric reducer depends on the specific application and the requirements of the piping system. Here are some guidelines:
Concentric Reducers: concentric reducers are used when an even or constant flow rate is required and when height restrictions are not a concern.
- Used when there is a need to maintain an even or constant flow rate throughout the piping system.
- Ideal for vertical pipes, where the reduction in size occurs gradually and evenly, without causing a buildup of fluid pressure.
- Typically used in applications where there are no height restrictions.
Eccentric Reducers: Eccentric reducers are used when the accumulation of air, gas, or solids needs to be prevented and when height restrictions are a concern.
- Used when there is a need to prevent accumulation of air, gas or solids in the piping system.
- Ideal for horizontal pipes, where the reduction in size causes a change in the centerline of the pipe, creating a low point that allows air, gas, or solids to be drained from the system.
- Typically used in applications where height restrictions are a concern, as they allow for a lower profile installation.
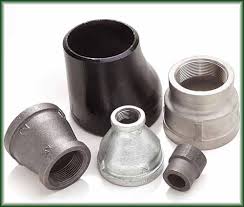
Study everything about piping reducers including types, codes, standards and pressure drop across pipe reducers.