Priming of a centrifugal pump is done by filling the pump with a liquid service that replaces air or other gases/vapor. This is done mainly to avoid the dry running of a centrifugal pump. This post explains the details of centrifugal pump priming.
Table of content:
What is priming in centrifugal pumps?
Why priming of centrifugal pump is necessary?
Centrifugal pump priming methods
How to prime centrifugal pumps
Troubleshooting priming issues
What is priming in centrifugal pumps?
Priming in pumps refers to the process of filling the pump casing and suction piping with liquid before the pump is started. This is done in order to remove any air or gases that may be present in the pump and suction piping, and to ensure that the pump is able to draw in and move the liquid efficiently.
Centrifugal pumps rely on the liquid being pumped to create a vacuum at the suction inlet, which in turn draws more liquid into the pump. If there is air or gas present in the pump or suction piping, it can prevent the pump from creating enough suction to draw in the liquid. This results in decreased flow rates and reduced efficiency.
Why priming of centrifugal pump is necessary?
Priming is important for centrifugal pumps because these pumps rely on the liquid being pumped to create a vacuum at the suction inlet, which in turn draws more liquid into the pump.
If a centrifugal pump is not properly primed before operation, several consequences can occur. First, the pump may not be able to create enough suction to draw in the liquid, resulting in low flow rates and decreased efficiency. This can also cause cavitation, which occurs when air or gas bubbles form and collapse within the pump, causing damage to the impeller and other internal components.
Additionally, if the pump is not primed properly, it may run dry, which can cause the seals and bearings to overheat and wear out quickly. This can result in costly repairs and downtime for the pump. Therefore, priming is an important step in the operation and maintenance of centrifugal pumps to ensure they function properly and efficiently.
Centrifugal pump priming methods
There are different methods of priming centrifugal pumps, including manual priming, automatic priming, and vacuum priming. The specific method used depends on the pump's design and application. These methods have been discussed here.
- Manual priming: This involves manually filling the pump casing and suction piping with liquid before starting the pump. This is typically done using a bucket, hose, or other liquid source.
- Automatic priming: Automatic priming systems use an external liquid source, such as a separate pump or vacuum system, to fill the pump casing and suction piping with liquid. This method is often used for larger pumps or applications where manual priming is not practical.
- Vacuum priming: This method uses a vacuum system to create a vacuum in the pump casing and suction piping, which draws in the liquid to prime the pump. Once the pump is primed, the vacuum system is shut off and the pump is started.
- Self-priming: Some centrifugal pumps are designed to be self-priming, meaning that they are able to draw in the liquid and remove air or gases without the need for external priming methods. Self-priming pumps typically have a built-in chamber or mechanism that allows them to create a vacuum and draw in the liquid.
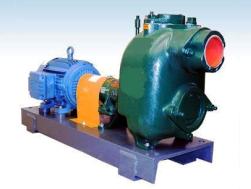
Check this post to explore what self priming pumps are, what makes them self priming, what is the role of recirculation flow and what are the variations in pump recirculation.
The specific method used to prime a centrifugal pump depends on the pump's design and application, as well as the availability of liquid sources and vacuum systems. Proper priming is essential for efficient operation and to prevent damage to the pump's internal components.
How to prime centrifugal pumps
A. Prime the pump with the suction supply above the pump
- Slowly open the suction isolation valve.
- Open the air vents on the suction and discharge piping until the pumped fluid flows out.
- Close the air vents.
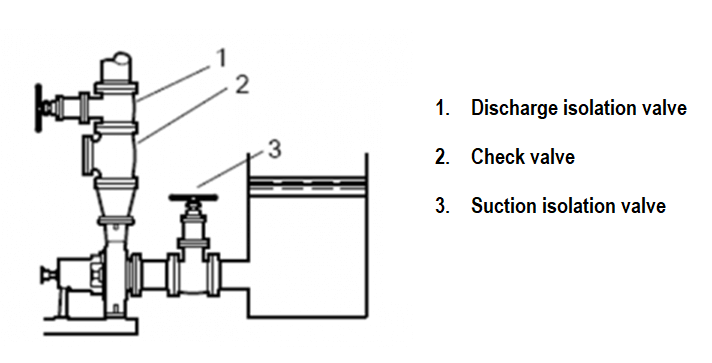
B. Prime the pump with the suction supply below the pump
Use a foot valve and an outside source of liquid in order to prime the pump. The liquid can come from one of these sources:
• A priming pump
• A pressurized discharge line
• Another outside supply
Typical steps for pump priming
- Close the discharge isolation valve.
- Open the air vent valves in the casing.
- Open the valve in the outside supply line until only liquid escapes from the vent valves.
- Close the vent valves.
- Close the outside supply line.
This illustration is an example of priming the pump with a foot valve and an outside supply:
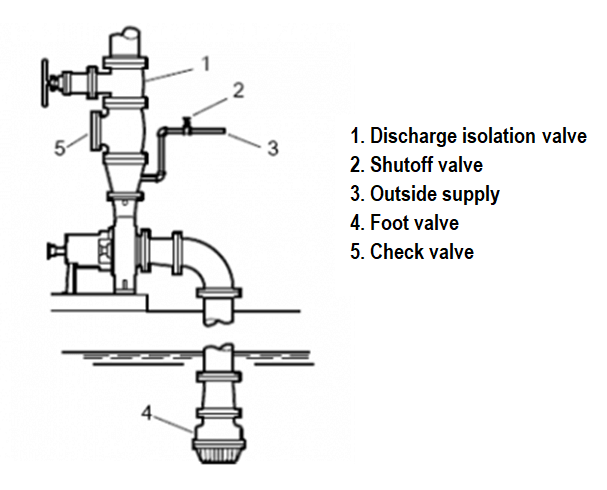
This illustration is an example of priming the pump with a foot valve using a bypass around the check valve:
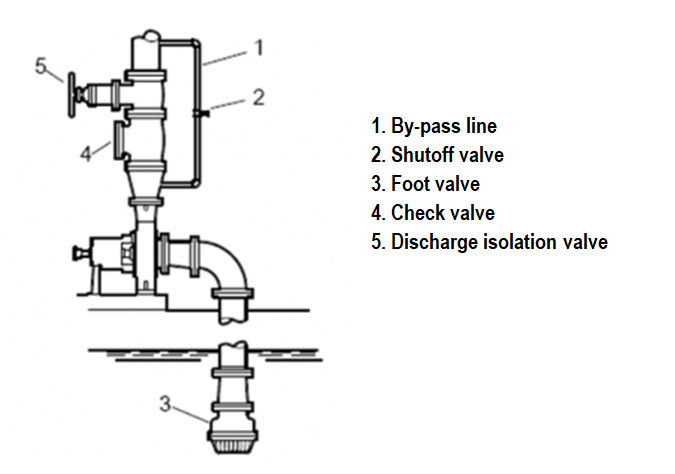
Check this post to understand working mechanism, design materials and use of foot valves in pumps.
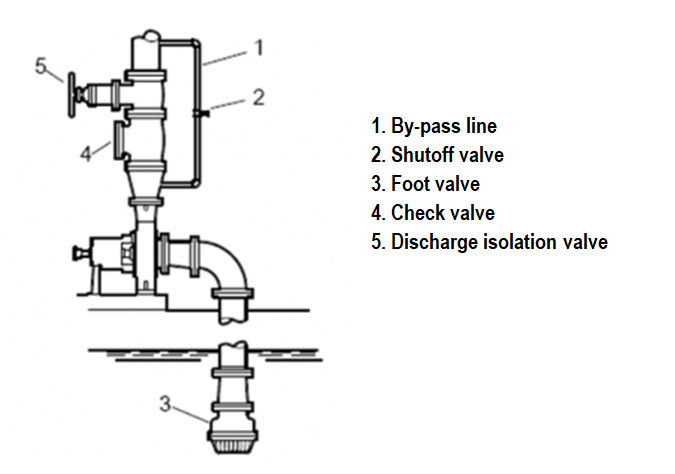
Troubleshooting priming issues
During the priming process, several common issues can arise that can affect the efficiency and performance of the centrifugal pump. Some of the common issues include air leaks, blockages, and cavitation.
Air leaks occur when air enters the pump casing or suction piping, preventing the pump from creating enough suction to draw in the liquid. This can cause reduced flow rates and decreased pump efficiency. To diagnose and troubleshoot air leaks, inspect the suction piping and pump casing for any cracks or leaks. Tighten any loose fittings or connections, replace damaged gaskets, and ensure that all valves are closed properly.
Blockages can also occur in the suction piping or pump casing, preventing the liquid from flowing into the pump. This can be caused by debris or foreign objects that become lodged in the piping or casing. To diagnose and troubleshoot blockages, inspect the suction piping and pump casing for any obstructions or debris. Remove any blockages and ensure that the suction piping is clear before priming the pump.
Cavitation occurs when the pump operates with low pressure or low flow rates, causing air or gas pockets to form and collapse rapidly, resulting in damage to the impeller and other internal components. To diagnose and troubleshoot cavitation, inspect the pump casing and suction piping for any obstructions or blockages that may be preventing the pump from operating at its designed flow rate and pressure. Adjust the discharge valve to ensure that the pump is operating at the correct pressure and flow rate, and check the pump impeller for any signs of damage.
In conclusion, diagnosing and troubleshooting issues during the priming process involves inspecting the pump casing and suction piping for any leaks, obstructions, or damage, and taking appropriate corrective measures to ensure efficient and proper operation of the centrifugal pump.
Check this post to study frequently occurring problems in pumps with the possible causes pertaining to them and steps to troubleshoot these issues. Check also this article about pump maintenance.