Pump priming is essential for the proper functioning of pumps. Priming refers to the process of removing air or other gases from the pump and the suction line, and filling it with the fluid that is to be pumped. This is important because air or gas in the pump can cause cavitation, which can damage the pump and reduce its efficiency.
Proper pump priming ensures that pump is operating efficiently and helping to prevent premature wear and tear. Therefore, understanding the concept of priming and implementing proper priming techniques is crucial for maintaining the reliability and efficiency of pumps in process industries.
Table of content:
1. What is priming of pump?
2.Why priming of pump is required?
3. Centrifugal pump priming
4. Why positive displacement pumps are self-priming?
5. Methods of priming
6. Priming the pump by installing a foot valve
7. Priming chamber
7. Prevention of un-primed pump operation
What is priming of pump?
Priming is the process of removing air or gas from the pump and the suction line, and filling it with the fluid that is to be pumped. The purpose of priming is to ensure that the pump is able to operate at its optimal capacity by ensuring that the pump is fully filled with fluid and there is no air or gas present in the pump.
Why priming of pump is required?
When air or gas is present in the pump, it can cause cavitation. Cavitation is the formation of bubbles or voids in the fluid that can collapse with great force when they come into contact with a solid surface, such as the impeller of the pump. This can cause damage to the pump and reduce its efficiency, leading to premature wear and tear. Priming reduces the risk of pump damage during start-up as it prevents the dry running of the pump.
For reliable operation, pumps must first be primed. That is, air or gases expelled from the suction and impeller eye area, and replaced with liquid. This is not a problem when the pump is submerged (submersible or vertical sump pumps) or when liquid supply is above the pump. However, when suction pressure is negative, air must be evacuated to accomplish pump priming. The self-priming pump is designed to insure that a sufficient quantity of liquid to re-prime is always retained in the priming chamber see the following figure.
By priming the pump, the fluid fills the pump and suction line. This displaces any air or gas present in the system. This ensures that the pump is able to operate smoothly and efficiently, without the risk of cavitation or other issues caused by the presence of air or gas.
Centrifugal pump priming
Centrifugal pumps are specifically designed to pump liquids and are unable to handle gases. These pumps do not have the ability to suck liquid. Instead of it they push the liquid from the suction side to the discharge side. The pressure difference created by pushing the liquid to the discharge side, allows more liquid to enter the suction side of the pump. However, for this to happen, the suction line must be completely filled with liquid, a process known as priming. The centrifugal pump essentially pushes the liquid out, and the pulling effect is not as significant.
During the start-up of the pump, if any air pockets are present at the suction side, the pump will push the air. As a result, the air present in the suction side will try to expand, which will block the liquid from entering the centrifugal pump. Therefore, if the pump is not primed, the suction pressure created will not be sufficient to lift water.
A centrifugal pump priming is done when the passageways of the pump are filled with the liquid to be pumped. The liquid replaces the air, gas, or vapor in the passage ways. This may be done manually or automatically. Centrifugal pumps are usually filled with the liquid to be pumped before start-up of centrifugal pump. When filled with liquid, the pump is said to be primed.
Pumps have been developed to start with air in the casing and then be primed. This procedure is unusual with low-specific-speed pumps but is sometimes done with propeller pumps.
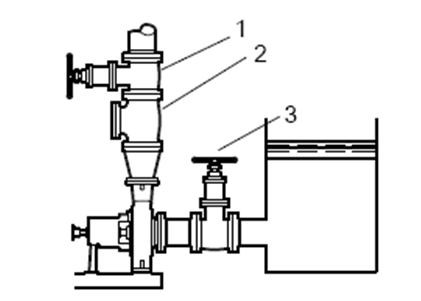
Follow these steps for priming of centrifugal pump.
Why positive displacement pumps are self-priming?
Positive displacement pumps work differently from centrifugal pumps. During the suction phase, the piston moves backward and creates a low-pressure zone in the pump. This pressure difference between the suction and storage tank is sufficient to pull the liquid, even if an air pocket is present in the suction line.
Positive displacement pumps create a high initial vacuum during the start of the suction stroke and are capable of evacuating all the air in their cylinder by virtue of their motion. This generates a better pressure or vacuum. Therefore, priming is not required for positive displacement pumps.
Methods of priming
There are several methods for priming pumps which are as discussed below.
Manual Priming: This method involves filling the suction pipe and pump casing with the liquid manually. The pump is then started, and the liquid is forced out of the discharge pipe.
Vacuum Priming: This method involves using a vacuum pump to create a vacuum in the suction pipe and pump casing. This vacuum draws the liquid into the pump, eliminating the need for manual priming.
Priming with jet pump: In this method, the jet pump is connected to the suction pipe and the discharge pipe of the centrifugal pump. When the jet pump is turned on, a high-velocity stream of water is forced through a nozzle. This creates a vacuum in the suction pipe. The vacuum created by the jet pump draws the liquid from the reservoir into the suction pipe of the centrifugal pump. The liquid flows through the pump and the impeller forces it out through the discharge pipe.
Priming with separator: A separator is a tank or vessel that is connected to the suction line of the pump. The process of priming with a separator involves filling the separator with the liquid being pumped and allowing it to settle. As the liquid settles, the air bubbles rise to the top of the separator and are removed through an air vent. The liquid is then allowed to flow from the separator into the suction line of the pump.
Priming by installing a foot valve: A foot valve is a type of check valve that is installed at the bottom of the suction line. Its purpose is to allow liquid to flow into the suction line while preventing it from flowing back out.
Priming the pump by installing a foot valve
Detailed procedure for priming by installing a foot valve method has been discussed here.
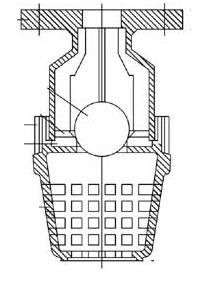
- A foot valve is a form of check valve installed at the bottom, or foot, of a suction line. When the pump stops and the ports of the foot valve close, the liquid cannot drain back from pump suction if the valve seats tightly. Foot valves were very commonly used in early installations of centrifugal pumps. Except for certain applications, their use is now much less common.
- A better method is to close a valve in the discharge line and prime by evacuating air from the highest point of the pump casing. Many types of vacuum pumps are available for this service.
- A priming chamber is a tank that holds enough liquid to keep the pump submerged until pumping action can be initiated.
- Self-priming pumps usually incorporate some form of priming chamber in the pump casing that must be filled with liquid in order to “self prime” the pump. Without this initial liquid charge filled in priming chamber, pump will not prime or pump. Self priming pump generally operate in an air-liquid mixture by transforming this mixture into a fluid that can be pumped without help of any external auxiliary devices. Priming chamber allows self priming pumps to recirculate liquid within the pump at will, ridding the pump of the air that prevents it from operating whenever necessary.
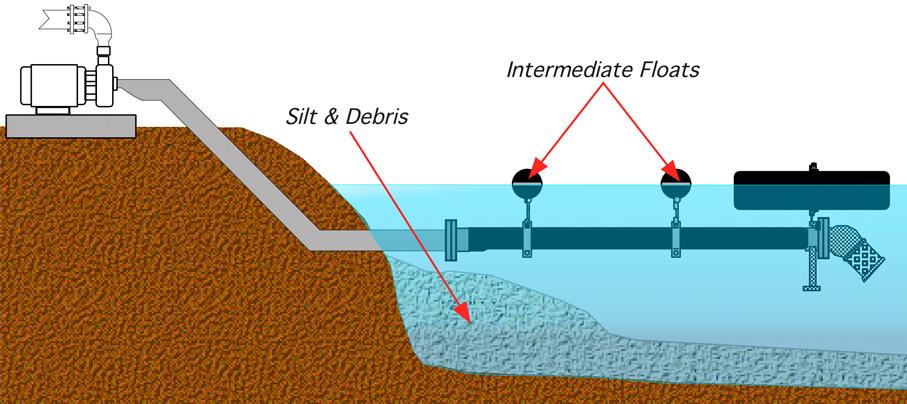
Above given schematic shows foot valve installation.
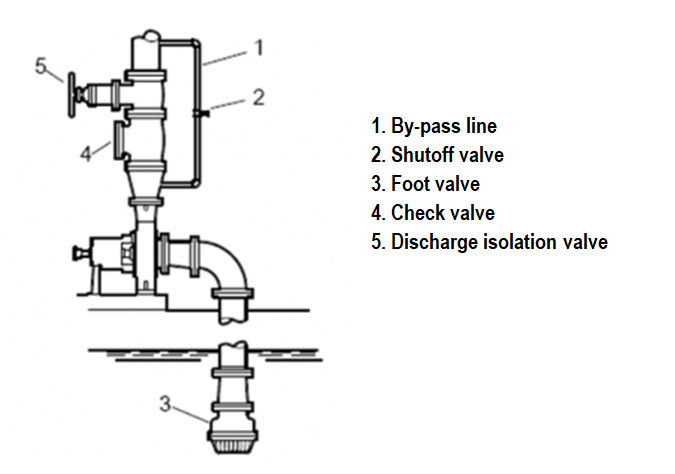
Check this post to understand working mechanism, design materials and use of foot valves in pumps.
Priming Chamber
A priming chamber is a device that is used to prime a pump. The priming chamber does this by creating a vacuum that draws the fluid into the pump. Priming chambers are typically made of metal or plastic and are available in a variety of sizes. They are typically installed between the pump and the suction line.
To prime a pump using a priming chamber, follow these steps:
- Fill the priming chamber with the fluid that will be pumped.
- Close the valve on the suction line.
- Open the valve on the priming chamber.
- Start the pump.
- Once the pump is running, open the valve on the suction line.
The priming chamber will create a vacuum that will draw the fluid into the pump. Once the pump is filled with fluid, the valve on the suction line can be opened and the pump will start pumping.
Here are some additional benefits of using a priming chamber:
- They can help to prevent cavitation, which can damage the pump.
- They can help to extend the life of the pump.
- They can help to improve the efficiency of the pump.
If you are using a pump that is located above the level of the fluid to be pumped, a priming chamber is a valuable tool that can help you to prime the pump quickly and easily.
Prevention of un-primed pump operation
Various methods are used to prevent the operation of a pump without being primed. The main aim of these methods is to ensure that the pump is completely filled with liquid before starting the operation. One such method involves the use of a float switch in a chamber connected to the suction line.
If the level in the chamber is above the impeller eye of the pump, the float switch control allows the pump to operate. If the liquid falls below a safe level, the float switch acts through the control to stop the pump, to prevent its being started, to sound an alarm, or to light a warning lamp. Such a valve and switch are illustrated in the following Figure