Preheating and welding of metal is a regular part of metal works.
Welding
Welding is basically the mixing of a base metal with filler metal. Filler material is melted at high temperature through a consumable electrode and provides the relevant bonding strength. Filler metal and base metal are bonded together in one solid body. A good quality weld is at least as strong as the base material(s) being joined.
Preheating
Preheating is a process performed before welding. It consists of gradually increasing the temperature of the filler metal. This way, thermal gradients-stresses are kept to a minimum and suitable mechanical properties and metallurgical structure can be established. Preheating also helps to eliminate the presence of moisture and hydrogen (this way, the danger of hydrogen embrittlement is minimised) from the Heat Affected Zone (HAZ). HAZ is generally the area of base material which had its structure and properties modified by welding. The weld itself is often termed as the fusion zone:more specifically, it is where the filler metal was applied during the welding process. Generally speaking, the metal in the Heat Affected Zone (HAZ) is often weaker than both the base material and the fusion zone.
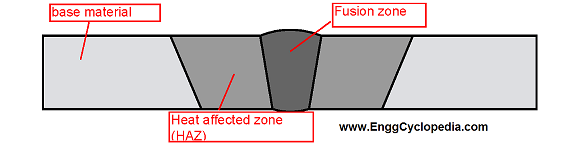
ASME B31.1 provides preheating requirements for power piping. In general, the bigger the carbon content, the alloy content and the thickness of the pieces to be welded, the bigger the necessity for preheating. Preheating can typically range from as low as 10 degrees Celsius to as high as 200 degrees Celsius or even more.
Preheating becomes more necessary and important when any of the following factors are present:
- Lower temperature of the pieces to be welded
- Low ambient temperature
- High speed of welding
- Significantly different masses of the pieces being welded
- Complicated geometries of the pieces being welded
Preheating is not necessary for 300 series stainless steels or nonferrous metals like nickel or aluminum.