As the name implies, different types of steam traps are installed in the steam carrying pipes to trap and remove steam condensate.
The basic role of steam traps is to remove steam condensate, air or other incondensable gases from a steam system, while at the same time not allowing live steam to escape.
Using the steam traps, steam can be made available in as dry a state as possible at the desired destination point, being either power generation (through a steam turbine), heating (i.e. for district heating applications) or any other industrial process application.
Besides condensate removal, air venting is another important task performed by steam traps. If air is not removed during start-up and mixes with steam, the only way the resulting mixture can be separated is by condensing the steam and vent the air to a safe system, something which is a clear waste of resources.
Types of Steam Traps
There are several types of steam traps in use nowadays. Each type has its advantages and disadvantages. Steam traps operating pressures can range from vacuum to hundreds of bars. It is critical that a detailed study is carried out for specifying and selecting a certain type of steam trap.
Most common types of steam traps used in industrial applications are the following:
Thermostatic steam traps
Thermostatic steam traps are operated using changes in fluid temperature. The temperature of saturated steam is dependent upon its pressure. In the steam space, steam provides its enthalpy of evaporation, thus producing condensate at steam temperature. Any further heat loss will cause the temperature of the condensate to drop. Thermostatic traps retain condensate until cooled to below saturation temperature. A thermostatic trap will pass condensate when this lower temperature is reached (sensed). As steam reaches the trap, the temperature increases and the trap closes.
As far as air venting is concerned, thermostatic steam traps are more advantageous compared to other types because they are fully open during start-up.
Mechanical steam traps
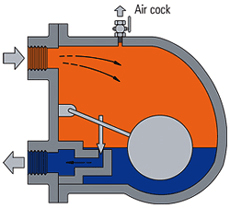
Mechanical steam traps are operated based on changes in fluid density. Mechanical steam traps work by sensing the difference in density between steam and condensate. Mechanical steam traps include ball float steam traps and inverted bucket steam traps.
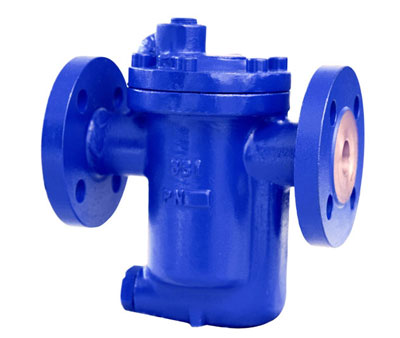
In a ball float steam trap, the ball rises when condensate is present, thus opening a valve which passes the denser condensate. In the inverted bucket trap, the inverted bucket floats when steam reaches the trap and rises to shut the valve. Both types are ''mechanical'' in their operation.
Thermodynamic steam traps
Thermodynamic steam traps are operated based on changes in fluid dynamics or changes in fluid pressure. Thermodynamic steam traps basically rely on the principle of formation of flash steam from condensate. Flash steam is the natural phenomenon occurring when hot condensate flows from a high pressure point to a low pressure point. As a result, a portion of the liquid boils and a mixture of steam and water is produced.
During startup, incoming condensate pressure lifts the disc, and cool condensate together with air is discharged (see step i of figure-3 below).
As the temperature of the condensate rises, hot condensate flows through under the disc. Consequently, its pressure is reduced and flash steam is produced. This high velocity steam creates a low pressure area under the disc, forcing it downwards (see step ii of figure-3).
At the same time, the flash steam pressure inside the chamber above the disc increases, pushing also the disc down against the incoming condensate . At this point, the flash steam is trapped in the upper chamber, and the pressure above the disc equals the pressure below the disc (see step iii of figure-3).
Finally, flash steam condenses and the pressure below the disc is bigger than the pressure above the disc. Thus, the disc is now raised and the cycle repeats (see step iv of figure-3).
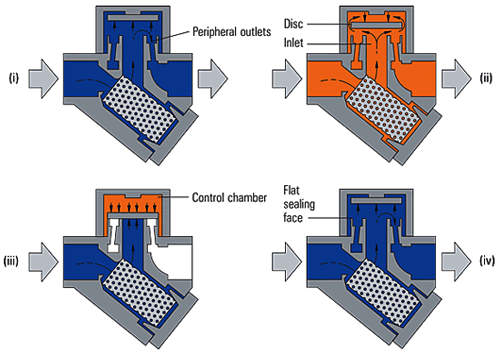
Air removal from a steam line
The most efficient way of air venting is with an automatic air valve. Air mixed with steam lowers the mix temperature. This allows a thermostatic steam trap (typical of the balanced pressure type) to vent the steam system. A balanced pressure steam trap consists of a capsule containing a special liquid. During start-up, the capsule is relaxed, the valve is off its seat thus allowing continuous removal of air.
For other types of steam traps, air venting is performed in other ways, most often by installing automatic air valves either parallel to the steam traps (if steam trap is installed at a steam line) or connected to the shell of the vessel (if steam trap is installed at the bottom of the vessel)
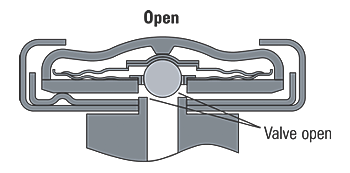