Outbreathing is the process by which gases or vapors are released from a storage vessel or container as a result of changes in temperature, pressure, or liquid level. Calculating the proper vent size and capacity for outbreathing is a critical aspect of ensuring the safe storage and transportation of liquids and gases. The venting calculation is done to ensure that the vent is properly sized to prevent overpressure or vacuum conditions that can lead to equipment failure or even explosions.
Table of content:
Breathing valve
Outbreathing valve
Venting calculation for outbreathing
Breathing valve
A breathing valve, also known as a pressure vacuum relief valve or a conservation vent, is a safety device used to prevent overpressure or vacuum conditions in storage tanks or vessels.
Breathing valves are typically installed on the top of tanks or vessels and consist of a valve and a pressure vacuum relief device. The valve allows gases or vapors to enter or exit the tank, depending on the pressure/vacuum conditions inside the tank. The pressure vacuum relief valve is designed to open automatically when the pressure inside the tank exceeds a certain level or when a vacuum condition occurs.
Breathing valves play a critical role in ensuring the safe and efficient operation of storage tanks and vessels. They help prevent damage to tanks or vessels due to overpressure or vacuum conditions that can occur during filling, emptying, or temperature changes.
Outbreathing valve
An outbreathing valve is a type of pressure relief valve that allows gas or vapor to exit a storage tank or vessel as the volume of liquid inside the tank increases due to filling or temperature changes.
As the liquid inside the tank is added or heated, the pressure inside the tank increases, which can cause an overpressure condition. If left unchecked, this overpressure condition can cause the tank to rupture or explode. An outbreathing valve allows gas or vapor to exit the tank to equalize the pressure and prevent an overpressure condition.
Outbreathing valves are typically installed on the top of tanks or vessels and consist of a valve and a pressure relief device. The valve allows gas or vapor to exit the tank as the pressure inside the tank increases, while the pressure relief device is designed to open automatically if the pressure inside the tank exceeds a certain level.
Venting calculation for outbreathing
Process tanks and vessels operating at low or atmospheric pressures are designed to handle low pressures and large variation in pressure can lead to damaging these equipments. Hence it is desirable to maintain these equipments at near atmospheric pressure (1.013 bara). This is done by providing a venting arrangement for inbreathing and outbreathing of air to protect against vacuum and overpressure respectively. The following information in this article pertains to protection of the low or atmospheric pressure storage tanks or vessels against overpressure, by outbreathing of air.
Process vessels and storage tanks containing liquid and gas can sometimes be subjected to build up of overpressure due to couple of reasons –
(i) liquid flow coming into the tank and thus compressing the gas
(ii) thermal expansion of the fluids (usually gas) inside the tank.
Due to these couple of reasons, the resultant volume expansion of gases in the tank leads to build up of pressure.
Overpressure in the tank can lead to possible structural damages and equipments need to be protected against such possibility. Protection can be provided by means of an open vent or a breathing valve. These devices will allow air to flow out, thus preventing pressure build up in the tank. The minimum required venting flow for the outbreathing can be calculated using guidelines from API 2000. Different possible scenarios with the corresponding sample venting calculations are discussed in the following sections.
Venting Calculation for Outbreathing due to liquid movement into the tank
As per API 2000, the outbreathing flow should be sized to correspond to maximum possible liquid flow into the tank. Depending on the flash point and normal boiling point of liquid contents at the tank operating pressure, the venting requirements are different.
For liquids with flash point above 1000F (37.80C) or normal boiling point above 3000F (148.90C) at tank operating pressure, the required venting flow is 6 SCFH (Standard ft3/h @ 15.6 0C and 1.014 bara) of air for each 42 US gallon barrel or 1.01 Nm3/h of air for each m3/hr of maximum liquid flow rate coming into the tank.
For liquids with flash point below 1000F (37.80C) or normal boiling point below 3000F (148.90C) at tank operating pressure, the required venting flow is 12 SCFH (Standard ft3/h @ 15.6 0C and 1.014 bara) of air for each 42 US gallon barrel or 2.02 Nm3/h of air for each m3/hr of maximum liquid flow rate coming into the tank. Thus for such liquids which are more likely to flash or to boil, the venting requirements are double. The additional 6 SCFH of air is based on 0.5 % of liquids being evaporated and vented along with air.
Venting Calculation for Outbreathing due to thermal expansion of gas
Temperature increase leads to pressure build up in the tank due to gases already present as well as evaporation from the liquid contents. Depending on the flash point and normal boiling point of liquid contents at the tank operating pressure, the venting requirements are different.
For liquids with flash point above 1000F (37.80C) or normal boiling point above 3000F (148.90C) at tank operating pressure, the required venting flow for outbreathing due to thermal expansion is 60 % of the corresponding venting flow for inbreathing due to thermal shrinking. The venting requirements for inbreathing due to thermal shrinking are discussed in EnggCyclopedia’s article about inbreathing venting calculation and also discussed in the following section.
For liquids with flash point below 1000F (37.80C) or normal boiling point below 3000F (148.90C) at tank operating pressure, the required venting flow for outbreathing due to thermal expansion is equal to corresponding venting flow for inbreathing due to thermal shrinking. This corresponds to 40 % extra flow compared to the higher boiling liquids. The venting requirements for inbreathing due to thermal shrinking are discussed in EnggCyclopedia’s article about inbreathing venting calculation and also discussed in the following section.
Venting Calculation for Inbreathing due to thermal shrinking of fluids
The venting requirements for inbreathing vary corresponding to the total tank capacity. For large capacity tanks the venting inbreathing requirements are directly proportional to the combined shell and roof area of the tank which is responsible for heat transfer out of the tank leading to thermal shrinking of the vapor contents. For tanks with capacity in excess of 20,000 barrels, the venting requirements are roughly 2 SCFH per ft2 of total shell and roof area. For smaller capacity tanks, the inbreathing flow requirement for venting is 1 SCFH of air per barrel of tank capacity, as per API 2000.
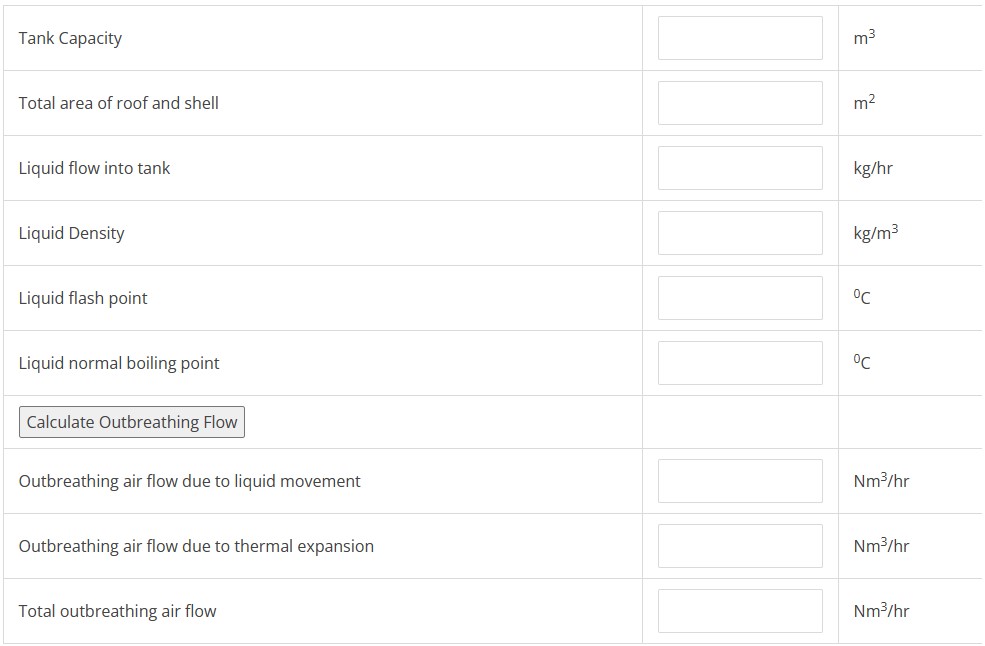
Normal Venting Calculator – Outbreathing Flow
Check Enggyclopedia's venting calculator for outbreathing flow.