Vibration in pumps is a common issue in pumps and can lead to various problems that can affect the performance, reliability, and safety of the equipment. When pumps vibrate excessively, it can lead to reduced efficiency, increased wear and tear, and premature failure of pump components.
Therefore, it is important to address pump vibration promptly and effectively. By monitoring and diagnosing the cause of pump vibration, maintenance personnel can take corrective actions. This will help ensure reliable and efficient pump operation, minimize downtime, and improve safety in the workplace.
Table of content:
What is vibration in pumps?
Types of vibration in pumps
Causes of pump vibration
Effects of vibration on pump performance
Pump vibration monitoring
How to prevent pump vibration
What is vibration in pumps?
Pump vibration is the rapid back-and-forth movement of the pump or its components, which can be caused by various factors such as unbalanced impellers, misaligned couplings, worn bearings, or other issues.
Vibration can cause impellers to wear out more quickly. This results in reduced pump flow and pressure. Excessive vibration can also cause damage to the bearings, seals, and other parts of the pump, leading to costly repairs or replacements.
In addition to these mechanical issues, pump vibration can also lead to noise and safety problems. Excessive vibration can create loud noise levels, which can be a nuisance or even a health hazard to workers in the vicinity. Moreover, if the vibration is severe enough, it can cause pump parts to detach or fail, resulting in potential safety hazards or accidents.
Types of vibration in pumps
There are three main types of vibration that can occur in pumps: radial, axial, and torsional. Each type of vibration has different causes and can affect pump operation in different ways.
- Radial vibration: This type of vibration occurs when the pump moves in a radial direction, perpendicular to the shaft. It can be caused by factors such as unbalanced impellers, bent shafts, worn bearings, and cavitation. Unbalanced impellers can create an uneven flow of fluid through the pump, while bent shafts and worn bearings can create an unbalanced load on the bearings. Cavitation can create uneven flow and pressure in the pump, leading to radial vibration.
- Axial vibration: This type of vibration occurs when the pump moves in an axial direction, parallel to the shaft. It can be caused by factors such as misalignment of the pump and motor shafts, worn thrust bearings, and hydraulic imbalances. Misaligned shafts can cause the pump to move back and forth in an axial direction, while worn thrust bearings can allow the shaft to move too far in either direction. Hydraulic imbalances can create uneven distribution of the fluid being pumped across the impeller, leading to axial vibration.
- Torsional vibration: This type of vibration occurs when the pump shaft twists or rotates. It can be caused by factors such as unbalanced rotating masses (such as impellers or flywheels) or torsional resonance, which occurs when the natural frequency of the pump shaft matches the frequency of the vibration.
Causes of pump vibration
It's important to identify the specific causes of pump vibration in order to take corrective action and prevent further damage to the pump.
- Unbalanced impellers: An unbalanced impeller can create an uneven flow of fluid through the pump, which can cause the pump to vibrate in a radial direction. The vibration caused by an unbalanced impeller can also cause excessive wear and tear on the bearings. This can lead to further vibration and damage.
- Misaligned couplings: A misaligned coupling between the pump and motor shafts can cause the pump to vibrate in an axial direction. This type of vibration can also cause excessive wear and tear on the thrust bearings.
- Worn bearings: Worn bearings can create excessive play in the pump shaft. This can cause the pump to vibrate in both radial and axial directions. The vibration caused by worn bearings can also cause further wear and tear on the bearings, which can exacerbate the problem.
- Cavitation: Cavitation occurs when air or gas bubbles form in the fluid being pumped, which can create an uneven flow and pressure in the pump. This can cause the pump to vibrate in a radial direction and can also cause damage to the impeller and other components.
- Hydraulic imbalances: Hydraulic imbalances can occur when the fluid being pumped is not evenly distributed across the impeller. This can cause the pump to vibrate in an axial direction and can also cause damage to the impeller and other components.
- Torsional resonance: Torsional resonance can occur when the natural frequency of the pump shaft matches the frequency of the vibration. This can cause the pump to vibrate in a torsional direction, which can cause damage to the shaft and other components.
Effects of vibration on pump performance
- Vibration can cause friction, wear and tear on the pump components, and increase energy consumption, all of which can reduce pump efficiency. This can result in increased operating costs due to higher energy usage and reduced output.
- Excessive vibration can cause damage to the pump components, including impellers, bearings, and seals. This can lead to reduced reliability and increased maintenance costs. In severe cases, vibration can even cause catastrophic failure of the pump.
- Vibration can also cause increased noise levels, which can be disruptive to nearby personnel and equipment.
- The increased wear and tear caused by vibration can reduce the lifespan of the pump, requiring more frequent repairs and replacements.
- Excessive vibration can also create safety hazards, such as leaks, overheating, and fires. This can pose a risk to personnel and equipment.
Pump vibration monitoring
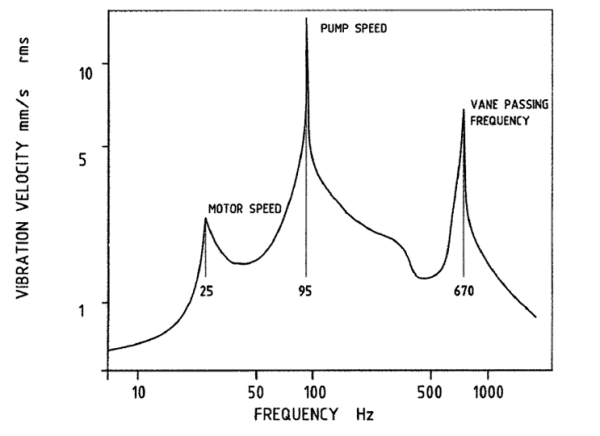
When it comes to assessing the mechanical integrity of centrifugal pumps, accelerometers can be applied to the bearing mount to detect excessive vibration. The frequencies of these vibrations can indicate the types of faults present, such as bad roller bearing elements or looseness due to worn out elements. By measuring two axes simultaneously, an overall mount movement can be detected if either the bearing or the mount is moving, and these frequencies occur proportional to the rotational speed. Vibration in centrifugal pumps can also be caused by shaft misalignment or weight asymmetry, which causes rotational forces proportional to the rotational speed.
For reciprocating or cyclic machines, such as reciprocating compressors, the vibration frequencies occur at the crankshaft rotational rate or natural frequencies in the mechanical vibration of the equipment. In these cases, shaft and component alignment can be checked using a proximity sensor to ensure mechanical tolerances are being met. It can be advantageous to measure vibration and proximity as a function of angle rather than time-based measurements, and a keyphasor or N/rev sensor can be used to align the angle-based data to a "zero degree" position in the cycle. This allows measurements to be associated with the position of moving parts, such as the vibration caused by an intake valve occurring at a different angle in the cycle than an exhaust valve.
In summary, using accelerometers, proximity sensors, and N/rev sensors can help in assessing the mechanical integrity of pumps, identifying faults and asymmetries, and ensuring that mechanical tolerances are being met. These tools are essential in diagnosing vibration issues and can help prevent significant damage to the pump and other equipment.
How to prevent pump vibration
- Proper installation of the pump and its components, including the motor and coupling, is essential in preventing vibration. The pump should be installed on a stable and level foundation, and the shaft alignment should be checked and corrected as necessary.
- Regular maintenance of the pump can prevent vibration issues by identifying and addressing potential problems before they cause significant damage. This includes checking and replacing worn components, monitoring vibration levels, and ensuring proper lubrication.
- Balancing the pump impeller is crucial in preventing vibration caused by unbalanced forces. The impeller should be balanced during installation and after any repairs or replacements.
- Proper alignment of the coupling is essential in preventing vibration caused by misalignment. The coupling should be aligned during installation and checked periodically during maintenance.
- The stiffness of the pump's foundation, support structure, and piping system can help prevent pump vibration caused by external forces and improve the pump's stability.
Pump vibration limits specify acceptable range of vibrations for different types of pumps. Check this post on pump vibration limits as per international standards.
Understand why pump vibration analysis is important for pump maintenance, how vibration monitoring and subsequent analysis is done using vibration analysis charts.
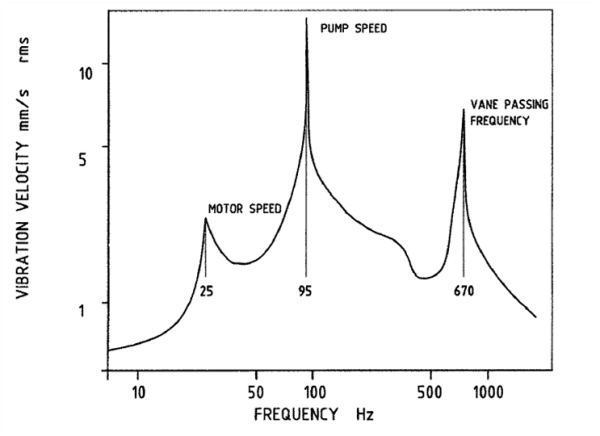