Pressure relief valves are commonly used for protection of equipment against internal over pressure. These valves allow fluid or gas to escape in over pressure conditions and release automatically excess pressure from equipment. Relief valves protect equipment and play important role in the industries to prevent hazards. This post explores some common terms of pressure relief valve and different types of pressure relief valve.
Table of content:
1. Important terms
2. Pressure relief valve types
2.1. Balanced bellows relief valve
2.2. Conventional pressure relief valves (PRVs)
2.3. Pilot operated relief valve
2.4. Power actuated pressure relief valve
2.5. Vacuum relief valve
Important terms
Before getting into the pressure relief valve types, some terms need to be described.
Superimposed back pressure
Superimposed back pressure is the static backpressure that exists on the outlet of the pressure relief valve, when the valve is closed. This pressure can be constant or variable depending on the conditions in the flare system before the relief valve can discharge.
Built-up back pressure
Built-up back pressure is the backpressure generated due to pressure losses at the outlet of an open relief valve when it is discharging. This pressure depends on the downstream pressure in the flare header to which the relief valve is discharging and the relieving flowrate which is being discharged.
When the relief valve is discharging, effects of superimposed and built-up back pressure exist together and felt as the combined back pressure.
Check this post to explore superimposed back pressure, built up back pressure and cold differential test pressure.
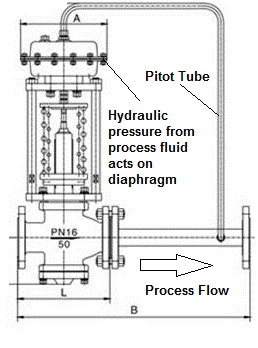
Pressure relief valve types
Following are the main pressure relief valve types commonly used in the industry.
Balanced bellows relief valve
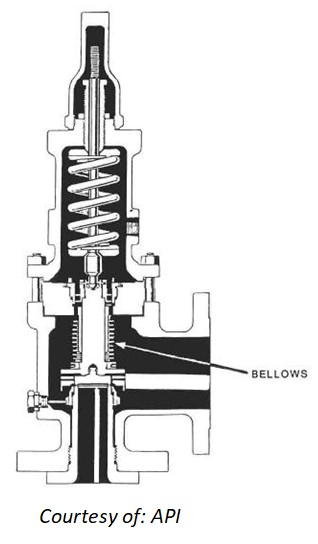
A balanced bellows relief valve uses bellows element to relieve excess pressure. The bellows act as sensing element and sealing element in these valves. The structure of balanced bellows valve consists of outer casing, bellows, spring and valve seat. The bellows is exposed to process fluid on one side and to reference pressure on the other side.
When the process fluid pressure increases, bellows expands. As a result, bellows exert a force against a spring mechanism and force exerted by bellows overcomes the force exerted by spring. This causes the valve seat to lift, allows the fluid to escape and relieve excess pressure.
Effect of back pressure on the operational characteristics of the valve is minimized by incorporating bellows. The bellows encircle an area equal to the inlet orifice area. This area is maintained free from the effect of back pressure from the discharge side of the relief valve. The space enclosed by bellows is freely vented to air. Thus the opposing pressure on the inlet fluid is generated by the spring alone without contribution from any sort of backpressure. For these relief valves allowable back pressure is 10 - 50% of the set pressure.
Advantage of using balanced bellows relief valves is no effect of back pressure on the relieving pressure and pressure accumulation. The spring is isolated from discharge fluid from the bellows, hence risk of corrosion mitigated. These relief valves get special consideration when there is high combined backpressure on the relief valve.
Disadvantage can be said to be the susceptibility of bellows to fatigue and failure and possibility of release of flammable or toxic process fluids being discharged to atmosphere through bellows vent.
Conventional pressure relief valves (PRVs)
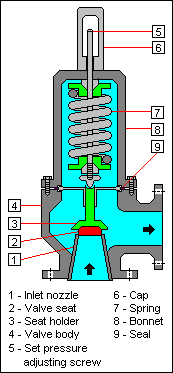
Conventional relief valves are also known as conventional spring loaded relief valve. These valves operate based on the force exerted by spring to maintain safe pressure. These valve consists of inlet & outlet port, valve disc, spring and valve body. Conventional relief valve senses the pressure at inlet port. When the pressure increases beyond set point, it acts against the force of spring. This causes the valve disc to open and allows excess pressure to escape.
Operational characteristics of this pressure relief valve are directly affected by back pressure changes. For conventional pressure relief valve, only the superimposed back pressure affects the opening characteristic and set pressure value, but the combined back pressure (superimposed backpressure plus built up backpressure) affects the blowdown characteristic and re-seat pressure value. A conventional pressure relief valve is not used when the built-up backpressure is greater than 10% of the set pressure at 10% overpressure. A higher maximum allowable built-up backpressure may be used for overpressure greater than 10%.
Advantages of conventional spring loaded relief valves are reliability and versatility. These relief valves are most reliable when sized properly and can be used in a wide range of services.
Disadvantage of these relief valves is the effect of backpressure on the relieving pressure of valve and hence pressure accumulation in the protected equipment. Also for high built up backpressure values generated by higher pressure loss in the relief valve discharge line, chattering can occur in these relief valves.
Pilot operated relief valve
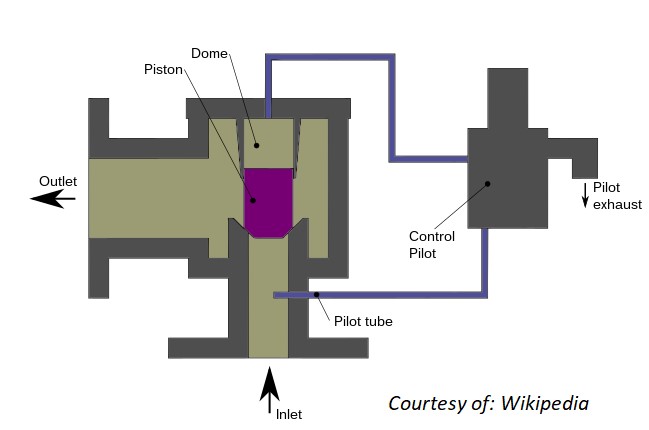
In pilot operated setup, main relief valve is combined with and controlled by a smaller self actuated pilot valve. Opening and closing of the main valve is controlled by this small pilot valve. The main is valve is larger and responsible for relieving excess pressure from the system.
This relief valve uses the process fluid itself, circulated through a pilot valve, to apply the closing force on the safety valve disc. The pilot valve is itself a small safety valve with a spring. The main valve does not have a spring but is controlled by the process fluid from pilot valve. This arrangement allows operation of pilot operated valves with a very narrow margin between set pressure of the relief valve and operating pressure of the protected equipment.
Hence these relief valves are particularly used for services where relief valve inlet line pressure drop is high (typically higher than 3% of set point) or when back pressure is high. Allowable back pressure is typically more than 50% of the set pressure.
Disadvantage of using pilot operated relief valves can be blockage of the pilot valve inlet outlet tubing by foreign matter such as hydrate, ice, wax etc.
Power actuated pressure relief valve
Compared traditional PRV which uses system pressure to open and close the valve, Power actuated relief valve uses external source for power such as electric motor or hydraulic actuator to open and close the valve. These types of valve allows for more remote operation and control. It consists of valve body, spring mechanism, an actuator and control system. The actuator applies force to overcome pressure exerted by spring or spring tension. As a result, valve opens and allows gas or liquid to escape to relieve pressure.
Vacuum relief valve
Vacuum relief valves are designed to protect the system from excessive vacuum or negative pressure conditions. This pressure relief valve type is used to admit external fluid to prevent an excessive internal vacuum. It allows atmospheric air or fluid to enter into the system when system pressure drops below a predetermined set point. Thus it maintains sufficient pressure in the system.