Globe valves are most widely used control valves in process industries to regulate the fluid flow through the pipelines. The name globe valve is derived from the shape of the valve, which resembles a globe or sphere. In this post, we will explore parts and working mechanism of a globe valve along with advantages, disadvantages and application.
Table of content:
1. What is a Globe Valve?
2. Parts of a Globe Valve
3. Working Mechanism
4. Types of Globe Valve
5. Advantages of Globe Valves
6. Disadvantages of Globe Valves
7. Applications of Globe Valves
What is a Globe Valve?
Globe valves have proved to be very popular recently since the globe valve design allows very fine regulation characteristics. They are very popular to be used as control valves. The name 'globe valve' originates from the spherical shape of the valve body.
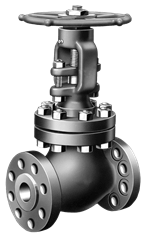
The globe valve body is divided into two halves by a partition or a baffle. These two halves can be connected by an opening at the center of the partitioning which divides the valve body in two halves. The globe valve consists of horizontal disc or plug that is closure member and a stationary ring seat. The disc is connected to a stem. This stem is operated by a actuator or handwheel. When the handwheel or actuator is turned, connected stem moves disc or plug up and down. This results in opening and closing of the valve eventually allowing or restricting the flow of fluid..
This design offers good regulation characteristics but causes more pressure drop across the valve due to high disturbance in the flow path. This pressure drop can be reduced to some extent by increasing the opening area in the partition to bring it up closer to cross sectional area of the pipe. Also, the partition can be angled in order to make the flow across the partition smoother and thus to reduce the pressure drop.
The discs in contact with the seat closes the valve. The seat can be damaged by formation of solid deposits. Hence globe valves are suitable only for clean service.
Parts of a Globe Valve
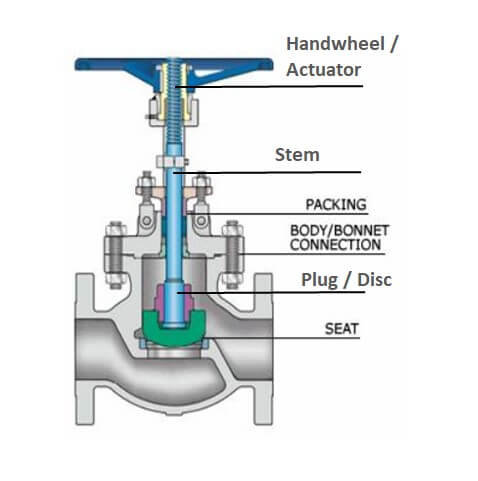
Disc or Plug : The disc or plug is movable component of the valve that controls the flow of fluid through a valve. It is connected to the stem and it can be moved up and down to regulate flow of fluid. The disc is spherical or conical in shape. The connection between the stem and the disc is threaded or welded connection depending on the design. The discs or the plugs in globe valves, which are the closure members can be available in wide variety.
Discs are not as effective as using plugs for throttling. For vapor service, discs cannot provide positive isolation, unless they are made of a resilient material.
The plugs for globe valves are also available in a wide variety from needle shape to semi-disc shape. The contour of the plug can be designed to specifically achieve the desired throttling characteristic. For example, needle shaped plugs are finest for flow control.
Seat : The seat provides surface for the shut off of the valve. The seat is stationary ring surface against which the disc or plug seals when the valve is in closed position. The seat ensures tight shut off which prevents leakage when the valve is closed. The shape of seat is designed to match the disc or plug for proper sealing. It is typically made of resilient materials such as soft metal or Teflon.
The seat can be damaged by formation of solid deposits. Hence globe valves are suitable only for clean service. The seats for discs or plugs can either be integrated with the body or can be screwed or welded to it. Depending on the application and service, wide range of materials can be used for the seat rings.
Stem : The stem is a rod like component and acts as a connector between the valve disc and actuator. When the handwheel or actuator is operated it causes stem to move. This results in moving of the disc or plug to regulate the flow. Stems can be smooth for actuator operated valves or it can be threaded for manually operated valves.
Body : Main outer shell that contains internal components is called body of the globe. The body of a globe valve is designed to withstand temperature and pressure of the application. Body contains inlet and outlet valve for entry and exit of the fluid into a valve. These ports are generally straight allowing straight flow. In some cases these ports are angled at 90 degrees, which are named as angled globe valves.
Bonnet : Bonnet is a cover that fits over a valve body and seals valve body to provide leak proof closure. The stem passes through bonnet. The bonnet is essential for preventing and leakage and protecting stem. The bonnet may contain additional features such as packing or sealing arrangement to ensure secure seal around the stem. The bonnet also provides access to the valve internals for maintenance and repair.
Working Mechanism
When the valve is in fully open position the disc is lifted away from the seat. In this position there will be unobstructed flow path for the fluid to pass through a valve.
To close the globe valve actuator or handwheel is operated such that stem is rotated clockwise. This causes the disc to move downward and tightly seal against the seat. In this position any fluid flow through valve will be prevented.
Apart from these two position globe valves can be used for throttling by partially opening or closing the valve. Flow of fluid can be controlled at various levels. The degree of throttling or fluid regulation depends on the position of the disc. As the disc moves up or down the effective flow area changes, which results in increased or decreased flow rate. This throttling capability of globe valves is particularly useful in applications where precise control on flow is required.
Types of Globe Valve
There are several types of globe valves, each designed for specific applications and operating conditions. Here are some common types of globe valves.
T-Type Globe Valve
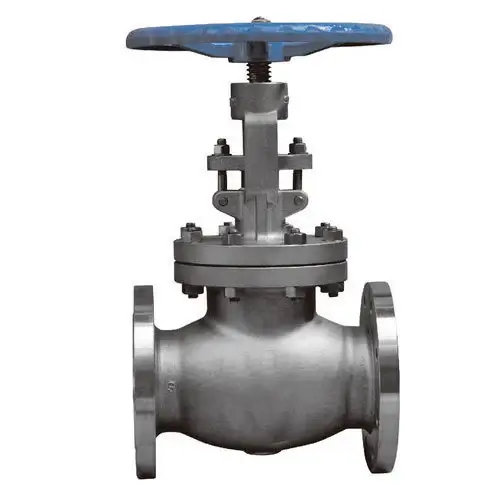
T-type globe valves have a T-shaped flow path, with the fluid entering from one side and exiting through the opposite side. This design allows for smooth flow and reduced pressure drop. T-type globe valves are suitable for applications requiring minimal turbulence and low pressure drop.
Y-Type Globe Valve
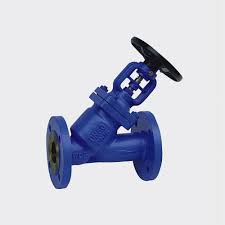
Y-type globe valves have a Y-shaped flow path, with the fluid entering from one side and passing through a branch outlet at an angle. This design helps in reducing the pressure drop and prevents clogging by trapping any solid particles or debris in the branch outlet. Y-type globe valves are commonly used in applications where the fluid may contain contaminants.
Angle Globe Valve
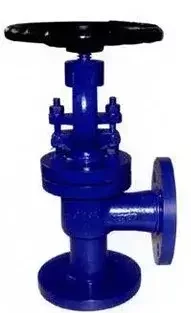
Angle globe valves have an angled flow path, with the inlet and outlet at 90 degrees to each other. This design allows for easy installation in pipelines where space is limited or when there is a need to change the direction of flow. Angle globe valves are commonly used in applications where a high-pressure drop needs to be controlled.
Advantages of Globe Valves
Globe valves are best known for the throttling capacity. They also have good shut-off capacity. Compared to gate valves they have shorter stroke.
- Precise Flow Control: Globe valves offer excellent flow control capabilities, allowing for precise adjustment of the flow rate. The ability to position the disc at intermediate points enables fine-tuning of the flow, making them suitable for applications that require accurate regulation of fluid movement.
- Tight Shut-off Capability: When fully closed, globe valves provide a reliable shut-off, minimizing leakage and preventing the passage of fluid. The disc tightly seals against the seat, ensuring a tight closure and maintaining system integrity. This feature is crucial in applications where complete cessation of fluid flow is necessary for safety or operational reasons.
- Versatility in Handling Different Fluids and Pressures: Globe valves are versatile and can handle a wide range of fluids, including liquids, gases, and even slurries. They are available in various materials, allowing them to withstand different fluid properties, corrosive environments, and temperature ranges. Additionally, globe valves are designed to handle high pressures, making them suitable for demanding industrial applications.
Disadvantages of Globe Valves
- Pressure Drop Across the Valve: The torturous path of the flow through a globe valve causes a larger pressure drop compared to other valves. Due to the change in flow direction and the narrowing of the flow path when the disc is partially closed, globe valves can create a pressure drop across the valve. This pressure drop can impact the overall system performance and efficiency. Careful consideration should be given to system design and valve sizing to minimize the pressure drop.
- Limited Suitability for High-Velocity Applications: Globe valves are not ideal for high-velocity flow applications. The change in flow direction and the presence of the disc can cause turbulence and pressure fluctuations at high flow rates. In such cases, other types of valves, such as ball valves or butterfly valves, may be more suitable.
- Also, to close the valve, the disc needs to be seated with opposition from flow under the seat. Hence great force or a large actuator is needed to operate the valves.
Applications of Globe Valves
Flow control for cooling water systems, fuel oil systems and other service where flow regulation is important: Globe valves are often used to control the flow of fluids in cooling water systems, fuel oil systems, and other applications where precise flow control is important. Globe valves can be used to regulate the flow of fluids in a wide range of applications, including:
- Cooling water systems
- Fuel oil systems
- Chemical feed systems
- Steam systems
- Air conditioning systems
- Process control systems
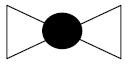
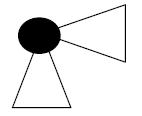
Vents and drains requiring leak tight valves: Globe valves are often used in vents and drains because they provide a leak-tight seal. This is important in vents and drains because any leaks could contaminate the environment or cause other problems. Globe valves are often used in the following types of vents and drains:
- Boiler vents
- Condensate drains
- Oil tank vents
- Chemical feed tank vents
- Air compressor drains
Control valves applications: Globe valves are often used in control valves because they provide a precise and reliable way to control the flow of fluids. Control valves are used in a wide range of applications, including:
- Heating and cooling systems
- Process control systems
- Pharmaceutical manufacturing
- Food and beverage processing
- Chemical manufacturing