Axial compressor works by compressing and accelerating a gas or air, as it passes through a series of rotating and stationary blades in a cylindrical shape. This process is essential for producing the high pressures and flow rates required for these applications.
This post contains an overview of axial compressors including their working, advantages, disadvantages, as well as their various applications.
Table of content:
1. What is an Axial Compressor?
2. Axial Compressor Working
3. Axial Compressor Design
4. Advantages of Axial Flow Compressor
5. Disadvantages of Axial Flow Compressor
6. Applications of axial compressor
What is an Axial Compressor?
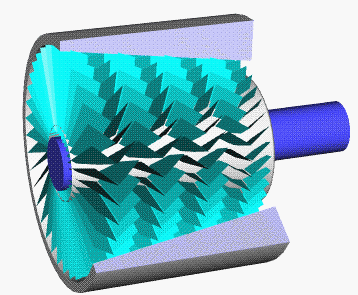
Axial compressors accelerate the flow of air through a series of rotating and stationary blades, increasing their pressure and temperature in the process. In an axial compressor, air or gas flows through the compressor in an axial direction which is parallel to the axis of rotation of the compressor.
The axial flow of air through the compressor allows for high compression ratios and make them highly efficient. This makes them ideal for use in gas turbines and jet engines, where they are used to compress the incoming air before it is mixed with fuel and ignited in the combustion chamber.
Axial Compressor Working
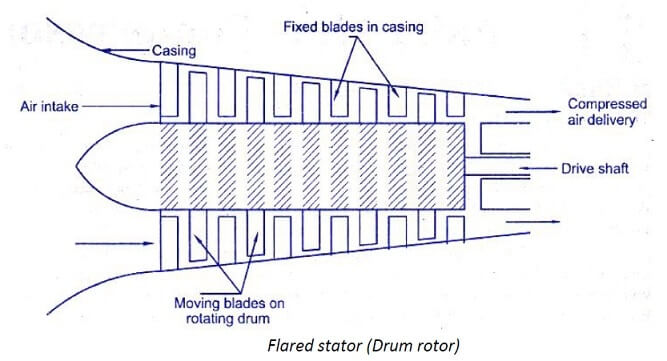
The working of an axial compressor can be explained in the following steps:
- Air or gas enters the compressor through the inlet and flows axially along the axis of rotation of the compressor.
- Axial compressor is divided in multiple stages. Each stage consists of series of rotating blades called rotor and series of stationary blades called stator. The rotor blades accelerates the gas and transfers kinetic energy to it, while the stator blades redirect the flow and increase the pressure of gas.
- The compressed gas then enters the next stage, which consists of another rotor and stator. This process is repeated for multiple stages, each stage increasing the pressure and temperature of the air.
- As the air passes through the compressor, it gains kinetic energy, which is converted into pressure energy by the stator blades.
- Finally, the compressed air leaves the compressor through the outlet and is then used for various applications such as combustion in gas turbines or for air supply in industrial processes.
Axial Compressor Design
The design of an axial compressor is critical to its efficiency and performance. The primary design considerations for an axial compressor include the number of stages, the blade geometry, the inlet and outlet shapes, and the materials used for construction.
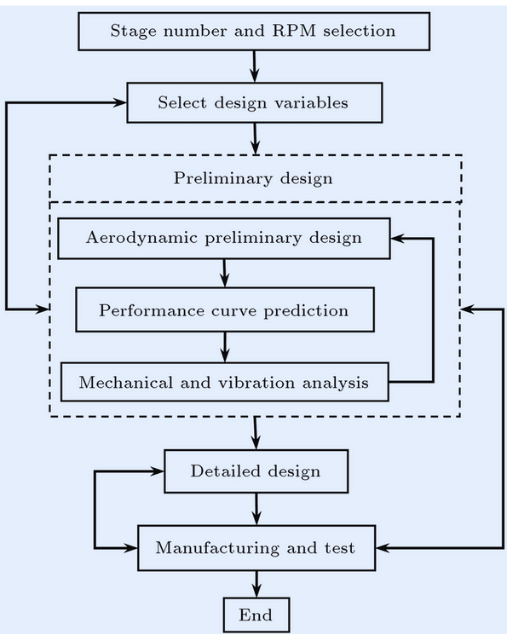
Courtesy of : Researchgate.net
Here are some of the key design features of axial compressors:
Number of Stages: The number of stages in an axial compressor affects its compression ratio and efficiency. Single-stage compressors have a low compression ratio, while multistage compressors can achieve high compression ratios. Typically, axial compressors have between 3 and 16 stages.
Blade Geometry: The shape and angle of the blades are critical to the performance of the compressor. The rotor blades are designed to accelerate the air or gas, while the stator blades redirect the flow and increase the pressure. The blade angles must be carefully optimized to achieve maximum efficiency.
Inlet and Outlet Shapes: The shape of the inlet and outlet ducts also affects the efficiency of the compressor. A smoothly contoured inlet and outlet can reduce turbulence and improve the flow of air or gas through the compressor.
Materials: The materials used for construction of the blades and other components must be able to withstand the high temperatures and stresses generated by the compression process. Modern axial compressors are typically made from advanced materials such as titanium alloys and high-temperature ceramics.
Cooling: The high temperatures generated by the compression process can cause thermal stresses and reduce the lifespan of the compressor. To prevent this, axial compressors are often designed with cooling channels or use advanced cooling techniques such as film cooling to dissipate heat.
Advantages of Axial Flow Compressor
Axial compressors offer several advantages over other types of compressors, including:
- Axial compressors can achieve high compression ratios with high efficiency, making them ideal for use in gas turbines, jet engines, and other industrial applications where high power output and efficiency are critical.
- Axial compressors are typically more compact and lighter in weight than other types of compressors, making them well-suited for use in aircraft and other applications where space and weight are limited.
- Axial compressors can handle high flow rates of air or gas, making them ideal for applications that require large volumes of compressed air or gas.
- The design of axial compressors minimizes vibration and noise, making them ideal for use in environments where noise and vibration must be minimized, such as in aircraft engines.
Disadvantages of Axial Flow Compressor
Axial compressors also have some limitations and drawbacks that must be considered when selecting a compressor for a specific application.
- Axial compressors are typically more expensive to manufacture and maintain than other types of compressors, such as centrifugal compressors. This is due to their more complex design and the use of high-performance materials.
- Axial compressors have a limited operating range and can be less efficient at low flow rates. This can result in lower efficiency and performance in certain operating conditions.
- Axial compressors are sensitive to inlet flow disturbances, such as those caused by turbulence or variations in the air or gas flow rate. These disturbances can cause instability and reduce compressor performance.
- Axial compressors are more sensitive to damage from foreign objects, such as debris or particles, which can cause damage to the blades and other components.
Applications of axial compressor
The axial flow of air through the compressor allows for high compression ratios which makes them more suitable for use in gas turbines and jet engines. Here is a more detailed explanation of each application.
Gas turbine engines: Gas turbine engines use axial compressors to compress air before it is mixed with fuel and burned to produce power. The compressed air is then fed into a combustion chamber where it is mixed with fuel and burned. The hot gases produced by the combustion process drive a turbine that powers the compressor and generates electricity or propels the engine. Axial compressors are ideal for gas turbine engines because they can achieve high-pressure ratios and handle large volumes of air.
Jet engines: Jet engines use axial compressors to compress air before it is mixed with fuel and burned to produce thrust. The compressed air is then fed into a combustion chamber where it is mixed with fuel and burned. The hot gases produced by the combustion process drive a turbine that powers the compressor and generates thrust. Axial compressors are ideal for jet engines because they can handle a wide range of flow rates and achieve high pressure ratios at high speeds.
Turbochargers: Turbochargers use axial compressors to compress air before it is fed into an engine's combustion chamber. Turbochargers are commonly used in automotive and marine engines to increase power and efficiency. Axial compressors are ideal for turbochargers because they can achieve high pressure ratios and handle large volumes of air at a high speed.
Centrifugal vs Axial Compressors
Axial and centrifugal-type compressors typically fall into the category of rotodynamic compressors. Check this post for comparison of centrifugal and axial compressors, understand the difference between them and look at different uses cases.
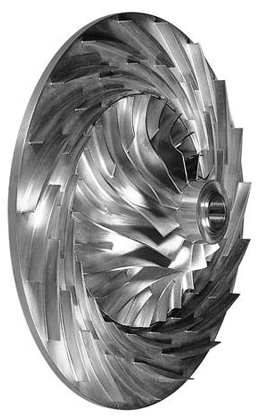