A demister pad, is a device used for removing entrained liquid droplets from a gas stream. As the name suggests the demister is used for removal of the mist from gaseous phase. Demisters are often fitted just below the top vapor outlet of a vapor liquid separator, as shown in the figure. Demister pads are also called as mist eliminators.
Demister pads or mist eliminators are a versatile and effective way to remove liquid droplets from gas streams. They are a valuable tool for improving the efficiency and safety of many industrial processes.
Table of Content:
1. How does a demister pad or mist eliminator work?
2. Demister example
3. Demister pad design calculation
4. Types of demisters
4.1. Wire mesh demisters
4.2. Vane type demisters
5. Suppliers for demisters
How does a demister pad or mist eliminator work?
Demister pads or mist eliminators are devices that are used to remove liquid droplets from a gas stream. They work by obstructing the path of the liquid droplets, which causes them to collide with each other and coalesce into larger droplets. These larger droplets are then too heavy to rise with the gas stream and fall back down to the bottom of the demister pad.
The obstruction of the liquid droplets can be achieved by a variety of geometries, such as a mesh type coalescer, vane pack, or other structure. The type of demister pad that is used will depend on the specific application.
Mist eliminators are used in a wide variety of industries, including chemical processing, petroleum refining, and pharmaceutical manufacturing. They are also used in air pollution control applications.
Mist eliminators are a valuable tool for improving the efficiency and safety of many industrial processes. They can help to reduce emissions, improve product quality, and extend equipment life.
Here are some additional benefits of using demister pads or mist eliminators:
- They can help to reduce the risk of explosions and fires.
- They can help to improve the quality of the final product.
- They can help to extend the life of equipment.
- They can help to reduce operating costs.
Demister example
For example, check the mesh like structure of a demister pad in the following image. This mesh is responsible for obstructing the flow of gas with liquid content. This way the liquid droplets come closer together, some of them coalesce into bigger drops and fall down - thus enabling better gas liquid separation.
Demister pad design calculation
Demister pads assist the empty drums by increasing the gas liquid separation efficiency. Empty drums rely on high residence time for separating liquid from vapor and require high sizes. By using demisters, the degree of separation can be achieved using smaller vessels. Demisters are often necessary to be used where any liquid entrainment in vapor stream is not acceptable, for example - compressor suction lines.
Vertical gas liquid separators are sized based on a design velocity for the gas phase which is described by the following equation,
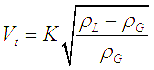
ρL and ρG are the densities of liquid and gas phase respectively.
K is a proportionality constant which depends on a number of factors which include liquid viscosity, surface tension, entrainment loading, and the content of dissolved and suspended solids. Recommended 'K' values are also highly dependent geometry of the demister and the vessel. The 'K' values for empty drum separator vessels can be improved 10 folds by using the appropriate demisters. High 'K' value means higher allowable gas velocities. Thus, for same design gas flow rate, vessel size (vessel diameter) can be reduced.
Here are a steps involved in the demister pad design calculations:
- Determine the liquid load to be separated from the gas or vapor stream.
- Obtain the droplet size distribution data to understand the range of droplet sizes present.
- Define the desired separation efficiency, which indicates the percentage of liquid droplets to be removed.
- Consider the pressure drop across the demister pad and ensure it remains within acceptable limits.
- Size the demister pad based on the gas flow rate, liquid load, and desired separation efficiency.
- Select appropriate mesh size and wire diameter based on the droplet size distribution and efficiency requirements.
Types of demisters
There are different types of demisters and several methods commonly used for demisting or removing liquid droplets from gas or vapor streams in separator vessels.
Wire mesh demisters
Wire mesh demisters consist of multiple layers of woven wire mesh. The mesh captures and coalesces the liquid droplets, allowing the gas or vapor to pass through. The captured liquid then drains back into the liquid phase below the demister. The efficiency of wire mesh demisters depends on factors such as mesh size, wire diameter, and pad thickness.
There are two main types of wire mesh demister pads: disk shaped and bar type. Disk shaped demister pads are typically used in applications where the liquid droplets are large and the gas stream is not very turbulent. Bar type demister pads are typically used in applications where the liquid droplets are small or the gas stream is very turbulent.
Here are some additional details about the two main types of wire mesh demister pads:
Disk shaped demister pads | Bar type demister pads |
---|---|
Disk shaped demister pads are made of a series of concentric disks that are connected by wire mesh. | Bar type demister pads are made of a series of parallel bars that are connected by wire mesh. |
The disks create a series of small channels through which the gas and liquid flow. The liquid droplets are trapped in these channels and prevented from flowing out with the gas. | The bars create a series of small channels through which the gas and liquid flow. The liquid droplets are trapped in these channels and prevented from flowing out with the gas. |
Disk shaped demister pads are typically used in applications where the liquid droplets are large and the gas stream is not very turbulent. | Bar type demister pads are typically used in applications where the liquid droplets are small or the gas stream is very turbulent. |
This is because the large liquid droplets are more likely to collide with the disks and coalesce into larger droplets. | This is because the small liquid droplets are more likely to collide with each other as they flow through the channels. |
Demister pads can be installed in two ways: upload and download. Upload demister pads are installed with the opening at the top of the pad. Download demister pads are installed with the opening at the bottom of the pad. The type of demister pad and the installation method that is used will depend on the specific application.
Here are some additional details about the two installation methods:
Upload demister pads | Download demister pads |
---|---|
Upload demister pads are installed with the opening at the top of the pad. | Download demister pads are installed with the opening at the bottom of the pad. |
This is the most common installation method for wire mesh demister pads. | This installation method is typically used in applications where the liquid droplets are small or the gas stream is very turbulent. |
Upload demister pads are typically used in applications where the liquid droplets are large and the gas stream is not very turbulent. | Download demister pads are typically used in applications where the liquid droplets are small or the gas stream is very turbulent. |
This is because the large liquid droplets are more likely to fall down to the bottom of the pad and collect in the pool of liquid below. | This is because the small liquid droplets are more likely to be carried away by the gas stream if they are not collected in the pool of liquid below. |
Vane type demisters
Vane-type demisters utilize a series of corrugated vanes or blades to remove liquid droplets. The vanes create a tortuous path for the gas or vapor flow, causing the droplets to impinge on the surface and coalesce. The coalesced droplets then drain back down into the liquid phase. Vane-type demisters are effective for high liquid load applications.
Suppliers for demisters
Here, you can find the details of demister pad suppliers who are listed on the EnggCyclopedia supplier's database. You can further contact them about your requirements.
If your business also makes or supplied demisters for industrial gas-liquid separation processes, you are welcome to register your details on our platform. So that more customers can find you.