An air-cooled heat exchanger is a type of heat exchanger that uses air as the cooling medium to transfer heat from one fluid to another. An air cooled heat exchanger, or ACHE, is simply a pressure vessel which cools a circulating fluid within finned tubes by forcing ambient air over the exterior of the tubes. A common example of an air cooler is a car’s radiator.
Table of Content:
1. What is an Air-Cooled Heat Exchanger?
2. Major Components
3. Types of Air-Cooled Heat Exchangers
4. Applications of Air-Cooled Heat Exchangers
What is an Air-Cooled Heat Exchanger?
Air-cooled heat exchangers are used to transfer heat from a fluid to air. The fluid flows through a series of tubes, while air is forced over the tubes to transfer heat.
The working principle of an air cooler is that they utilize the ambient air for cooling the fluids which have a significantly higher temperature than ambient air (around 150C). The hot fluid flows through finned tubes across which air is blown by fans. Depending on whether the fans are located above or below the tubes, the coolers can be classified as induced draft coolers or forced draft coolers respectively. Induced draft coolers pull the flow of air across tubes. Forced draft coolers with fans located below the tubes, push the flow of air across the tubes. The cooled fluid then flows back to the process or equipment that generated the heat, while the heated air is typically released into the atmosphere.
Major Components
The basic design of an exchanger involves four main components: a fluid circuit, an air circuit, a heat exchanger core, and a fan.
Fluid Circuit: The fluid circuit is the part of the heat exchanger where the process fluid, such as oil, water, or chemicals, flows through. The fluid is typically pumped into the heat exchanger through an inlet and exits through an outlet.
Air Circuit: The air circuit is the part of the heat exchanger where the air flows through. The air is typically drawn in by a fan and exits through an outlet.
Heat Exchanger Core: The heat exchanger core is the part of the heat exchanger where the heat transfer takes place. It is the place where the fluid and air circuits meet and the heat is transferred from the fluid to the air. The core can be made of different materials such as aluminum, copper, or stainless steel, and can come in different designs such as a finned tube, tube bundle, and plate-fin.
Fan: The fan is used to force the air through the air circuit. The fan can be a propeller fan, a centrifugal fan, or a blower, depending on the application.
Types of Air-Cooled Heat Exchangers
Forced draft type air cooler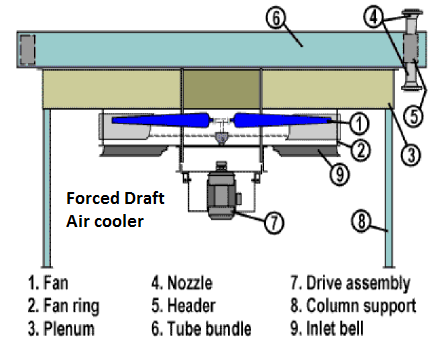
- Low power requirement for air Temperature rise greater than 100C.
- Adaptable for winterization, pour point Recirculation schemes.
- More readily accessible for maintenance.
- Exchangers are easy to remove for repairs.
- No mechanical equipment exposed to hot air. Whereas induced draft is subjected to much higher temperature.
- Less structural support required.
- Isolated support for mechanical equipments.
Induced draft type air cooler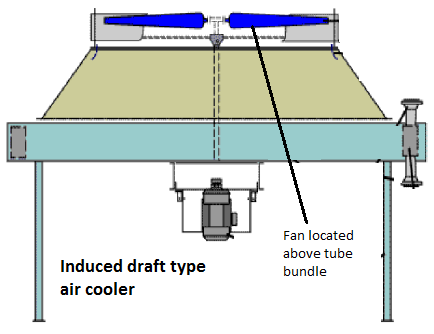
- Requires less power for an air temperature rise less than 10 oC.
- Less hot air circulation as exhaust air velocity Is about times that of forced draft.
- Offers bundle protection from adverse weather.
- Better suited for cases with close approach temperatures between inlet air & outlet fluid.
- Air distribution over exchanger is better.
- Will transfer more heat by natural convection because of stack effect.
- Connecting piping usually less
Types of tube bundle or manifold arrangements for air coolers
Applications of Air-Cooled Heat Exchangers
- Air-cooled heat exchangers are commonly used in industrial and power generation applications where large amounts of heat need to be dissipated, and where the availability of cooling water is limited or costly.
- In power generation, air-cooled heat exchangers are used to cooling the lubricating oil and hydraulic oil used in the turbine and generator components. They are also used to cool the transformer oil used in electrical substations. This helps to maintain the proper operating temperature for the equipment and prolong its lifespan.
- They are also used in natural gas processing plants to cool the gas before it is transported through pipelines
- Air-cooled heat exchangers are used in the petrochemical industry to cool process fluids, such as catalysts and reactor coolants, in the production of chemicals and plastics. They are also used to cool the fluids used in the distillation and refining process.
- They are also used in air-conditioning systems, where they transfer heat from the refrigerant to the outside air. In HVAC systems, air-cooled heat exchangers are used to cooling the refrigerant in air conditioners and chillers. They are also used to cool compressed air systems.
Advantages
- Air is always available.
- Maintenance cost normally less than for water cooled systems.
- In event of power failure they can transfer some heat because of natural convection.
- Mechanical design is normally simpler due to pressure on air side always being closer to atmospheric.
- Fouling on air side can normally be ignored.
- No problem arising from thermal & chemical pollution of cooling fluids.
Disadvantages
- Noise – Low noise fans are reducing this problem but at cost of fan efficiency & hence higher energy costs.
- May need special features for cold weather protection (high pour point liquids freezes in cold weather).
- Can not cool to same low temperature as cooling tower.