Overloading of pumps
Pump overloading occurs in centrifugal pumps when the driving motor draws excess current resulting in excess then normal power consumption. This overloading of the pumps can be caused by various reasons as discussed in one of the following sections.
Centrifugal pumps that are driven by AC induction motors should be started with minimum load on them so as to limit the starting current. Care has to be taken and certain procedures have to be followed while starting specific types of pumps to avoid high current being drawn by the motor at pump start-up. Therefore, it is recommended that radial impeller pumps be started with discharge valves closed whereas propeller pumps are started with discharge valves fully open. Centrifugal pumps with radial impellers, consume more power with an increase in flow rate. Thus, when the system resistance to the pump drops, more and more liquid is pumped resulting in increased power consumption. In such cases there is a tendency for the motor to trip on account of motor overload as shown in the following curve figure-1.
Pump hydraulic power requirement equation
Requirement of hydraulic power for operating a pump can be calculated using the following equation.
P (KW) =(Q*H*Sp.Gr)/(3.6*10^6)
Where: - “Q” is flow rate in m3.
“H” is head in meter fluid.
“ρ” Fluid density (Kg/m3).
"Sp.Gr.” Specific Gravity of the liquid (m/sec2).
Centrifugal Pump operation to the right of (Best Efficiency Point) BEP
Centrifugal pump operation to the right of the BEP has different set of problems as cavitation may occur, shaft may undergo deflection, mechanical seals and bearing can be stressed. This can cause a drop in pump efficiency and an increase in power consumption by pumps, which may cause the motor to trip.
The characteristic curves of the lower specific speed pumps indicate that such pumps have overloading features. Centrifugal pumps having low to medium specific speeds have P–Q curves which rise upward (curves 1 and 2 in figure-1). For higher specific speeds, the P–Q curves maybe approximately flat and horizontal. In case of propeller (axial flow) pumps, which have very high specific speeds, the power for the pump falls as the flow rate increases (curves 4 and 5 in figure-1).
This implies that for low specific speed pumps, the power requirement of the pumps keeps on increasing which ultimately leads to tripping and overloading of the motor.
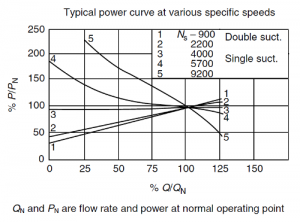
Pump suction specific speed (Nss ) is commonly used as a basis for estimating the safe operating range of capacity for a pump. The higher the Nss is, the narrower is its safe operating range from its best efficiency point (BEP). Most users prefer that their pumps have Nss in the range of 8000–11 000 for optimum and trouble-free operation.
Causes of Centrifugal pump overloading
Pump overloading may be caused by the motor drawing a high current due to the following reasons
- Speed too high
- Process liquid of higher viscosity.
- Oversized impeller installed
- Total head of system either higher or lower than anticipated
- Misalignment between pump and driver
- Rotating parts in contact with stationary parts
- Worn or damaged bearings
- Mechanical seal exerts excessive pressure on seat
- Bent shaft
- Pump operating too far out on head-capacity curve
Check this post for detailed discussion on causes of pump overloading.
The overloading of the pumps can negatively affect pump operation and life of the centrifugal pumps. The given post discuss these effects of pump overloading and how they can be prevented.
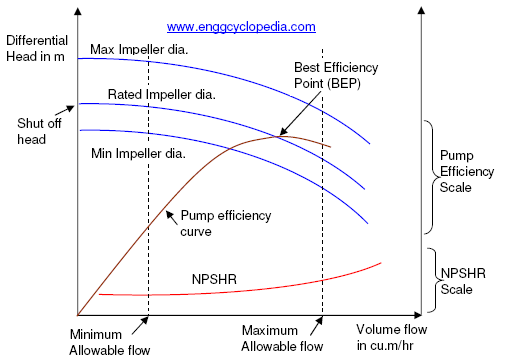