Control valves are used in the process industries to control the flow of fluid. Control valve actuators are integral components of the control valves. Valve actuators provide the necessary force or torque for the movement of the valve allowing it to restrict or open the valve opening.
Valve actuators accepts energy from different sources such as pneumatic or electric signal and converts it to mechanical motion. Thus actuators enables valves to respond to external signals such as electric, pneumatic or hydraulic signals and allows for the automated operation of the valves. The details of different types of valve actuators is explained in the given post.
Table of content:
1. Classification of control valve actuators
2. Manual valve actuators
3. Electric motor valve actuators
4. Pneumatic valve actuators
5. Solenoid actuated valves
6. Hydraulic actuators
7. Self actuated valves
Classification of control valve actuators
Control valve actuators can be classified either on the basis of type of motion generated by it or according to the source of energy accepted.
On the basis of type of motion generated valve actuators are classified into two categories.
1. Linear actuators : These types of valve actuators convert into linear motion to open or close the valve. This linear motion makes it suitable for linearly moving valves such as gate valves and globe valves. Linear actuators are capable of generating substantial amount of force which makes them suitable for heavy duty applications.
2. Rotary actuators : Rotary e actuators control the flow of fluid by converting energy to the rotary motion. This rotary motion makes them compatible with valve with rotary motion such as butterfly valve, ball valve or plug valve.
On the basis of source of energy accepted, valve actuators are classified into six types.
- Manual actuator (handwheel)
- Electrical motor operated actuators
- Pneumatic actuators
- Solenoid actuators
- Hydraulic actuators
- Self actuated
These valves are explained in detail in the given sections.
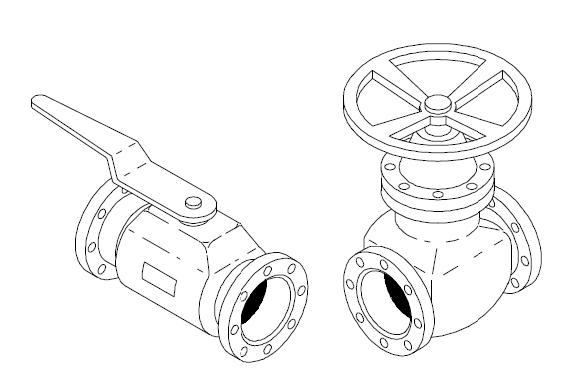
Manual valve actuators
Manual actuators are the most common type of valve actuators. Manual actuators are capable of placing the valve in any position but don't allow automatic operation.
Manual actuators include a handwheel connected to the valve stem either directly or through gears. Use of gears makes it easier to open or close the valve. However, several turns of gears are necessary for one full turn of the valve stem. This prolongs the opening and closing time of large sized valves.
Valves with handwheels directly fixed to the stem present the advantage of binding (sticking) when exposed to high operating temperatures. At these elevating temperatures, opening and closing of the valve becomes a rather tedious task.
Electric motor valve actuators
Electric motors allow manual operation (through a handwheel), semi-automatic operation (when the motor is started by a control system) and automatic operation of the valve. Automatic operation is achieved by connecting a motor to valve stem through a gear system. Use of the gear train allows to reduce motor speed and consequently to increase torque at the valve stem. Manual handwheel is also engaged in the gear train.
Motors are typically used for open-close (ON-OFF valves) duty. Automatic stoppage of the motor at fully open and fully closed valve positions is achieved through limit switches. Limit switches are activated either physically through the movement of the valve or torsionally by the motor torque.
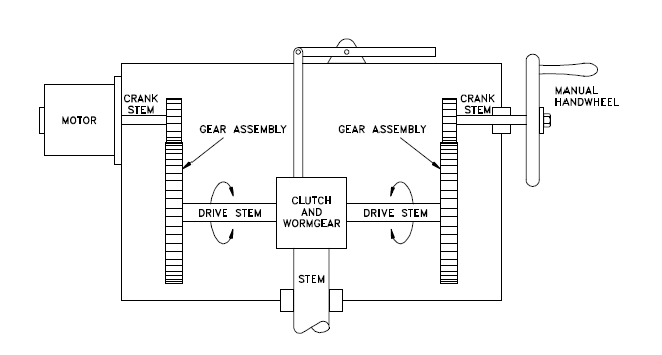
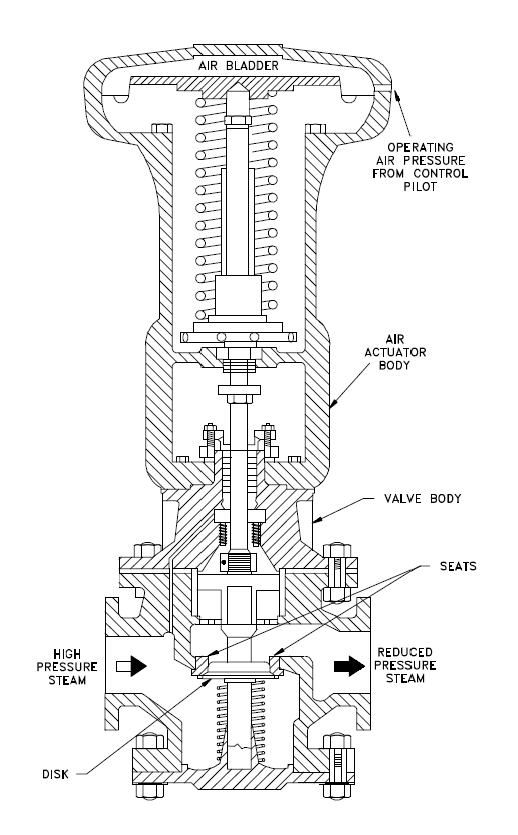
Pneumatic valve actuators
Pneumatic actuators provide for automatic or semi-automatic valve operation. They work by 'translating' an instrument air signal into valve stem motion by air pressure acting on a diaphragm or piston connected to the stem. The differential pressure across the diaphragm moves the valve stem. They are used when modulating (throttling) of the pumped fluid is necessary.
Pneumatic valves are also equipped with handwheels, limit switches as well as other instrument air related hardware, like for example air bottle and air filter regulator.
Solenoid actuated valves
Solenoid valves are typically used for automatic control of the hydraulic fluid to direct either opening or closing of the valve. They are mostly installed at small size lines, typically up to 1'' size. Solenoid actuators have a magnetic slug attached to the valve stem. The force to move the valve comes from the magnetic attraction that is developed between the slug on the valve stem and the coil of the electromagnet in the valve actuator. Solenoid actuated valves may be also equipped with manual override functionality in order to allow manual positioning of the valve for as long as the override is manually positioned.
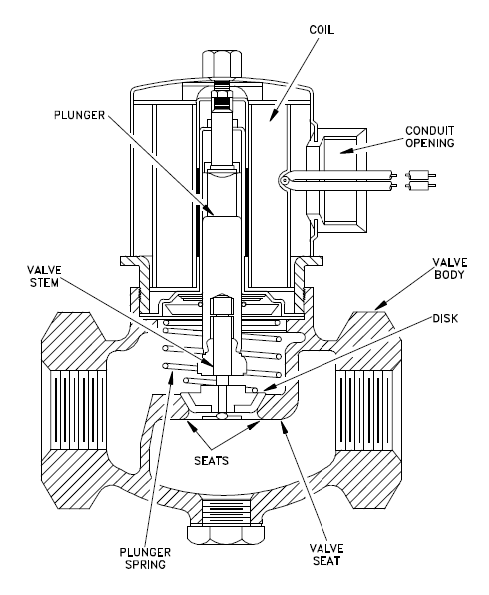
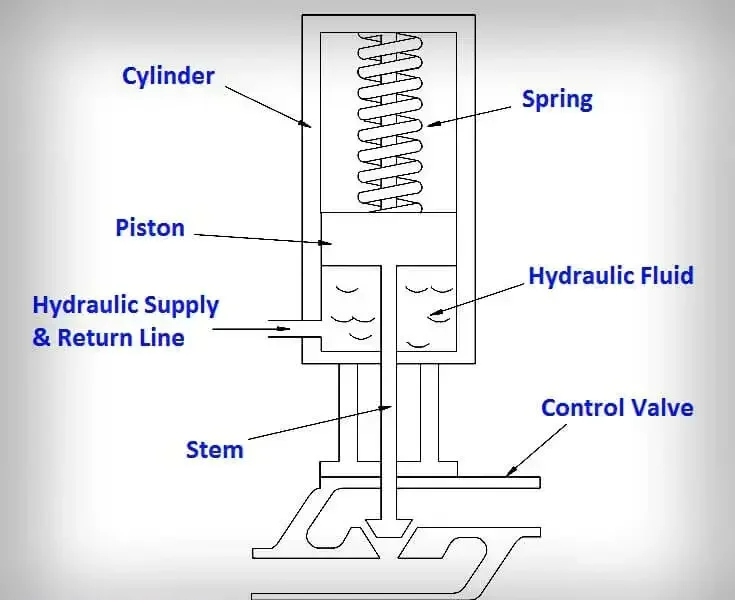
Hydraulic actuators
Similar to pneumatic actuators, hydraulic actuators enable semi-automatic and automatic operation. These actuators use a piston to convert a hydraulic signal pressure into valve stem motion. Hydraulic actuators use a pressurized liquid (typically oil is used as hydraulic fluid) on one or both sides of a piston to provide the force required to position the valve.
Self actuated valves
As their name implies, self-actuated valves make use of the system fluid itself to position-move the valve. No external power source is necessary for the operation of these valves. Typical examples of self-actuated valves are relief valves, safety valves and check valves. Check the given post to explore more about self actuated valves.
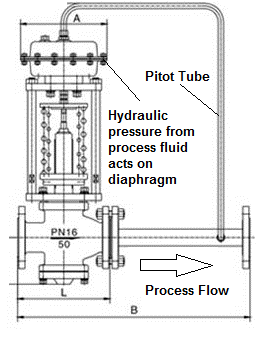