Heat transfer equipments are found to be useful in a wide range of industries. A heat exchanger is a device where two fluids of different temperatures flow through the same device in which transfer of heat takes place from high-temperature fluid to low-temperature fluid. It is important to study heat exchanger types because the structure and design of heat exchangers vary a lot depending on the application where they are used and the heat exchange media involved.
Heat transfer equipment can be classified into various types based on structure, phases of fluid involved, and the principle of operation.
Table of content
1. Plate and Frame Heat Exchanger
2. Spiral Heat Exchanger
3. Plate-Fin Heat Exchanger
4. Air coolers
5. Double Pipe Heat Exchanger
6. Shell and Tube Heat Exchanger
7. Kettle Type Heat Exchanger
8. Condenser
9. Evaporator
10. Regenerative Heat Exchanger
11. Twisted Tube Heat Exchanger
12. Scraped Surface Heat Exchanger
13. Coil Heat Exchangers
Plate and Frame Heat Exchanger
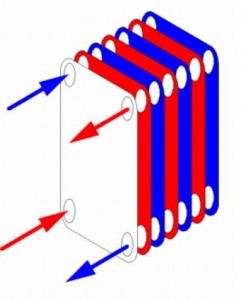
Plate exchangers are compact in structure and much cheaper compared to shell and tube heat exchangers. As shown in the schematic, these exchangers consist of a series of corrugated metal plates parallel to each other held together by gaskets located in the corners of each rectangular plate (indicated by holes in the following schematic). These gaskets also contain hot and cold fluids, indicated in the schematic by red and blue colors respectively. This series of plates form chambers that are alternatively filled with hot and cold fluids, so that each corrugated plate is separating hot and cold fluid providing a large area for heat transfer between these fluids.
The space between two plates determines the heat transfer coefficients and also the pumping cost. Although the pressure drop to push liquid through this space may be expected to be quite high, usually, the pressure drop per unit of heat exchanged turns out to be lower than that for shell and tube heat exchangers.
The major advantage of plate and frame heat exchangers is that they are relatively easy to disassemble, clean and reassemble. This makes them well-suited for applications where the fluids contain particles or where the fluids need to be cleaned frequently. They are also relatively compact and easy to install, making them well-suited for applications where space is limited.
These exchangers are well suited for applications where the fluids have a high fouling tendency or where the fluids need to be cleaned frequently. They are also well suited for applications where the fluids have different flow rates or where the fluids need to be heated or cooled separately. They are also ideal for use in applications where the heat exchange surface area needs to be increased or decreased easily.
This post contains a detailed study of plate and frame heat exchangers.
Spiral Heat Exchanger
A spiral heat exchanger is a type of heat exchanger that uses a spiral-shaped flow path to transfer heat between two fluids. The fluids flow in opposite directions through the spiral channels, which are typically made of metal such as stainless steel or titanium. The spiral shape of the channels increases the surface area for heat transfer and increases the efficiency of a heat exchanger.
Spiral heat exchangers are very basic in their structure. They consist of two separate spiral chambers as shown in the schematic above. These two chambers contain hot and cold liquids separated from each other by a spiral metal sheet. Heat transfer coefficients on both sides are high. The hot and cold fluid flows are countercurrent to each other through the exchangers.
Spiral heat exchangers are particularly useful in applications where one of the fluids is a gas and the other is a liquid, as the spiral design allows for large temperature differences between the two fluids without the risk of one fluid boiling or evaporating. They are also well-suited for high-pressure applications and also for the transfer of heat from hot gases to liquids.
One of the main advantages of spiral heat exchangers is that they are relatively compact, making them easy to install in tight spaces. They also have low maintenance requirements and can handle a wide range of fluid flow rates. However, they are relatively expensive compared to other types of heat exchangers such as shell and tube heat exchangers, and they may not be suitable for some applications where extremely high temperatures or pressures are required.
Spiral heat exchangers are typically used in industrial applications where high heat transfer rates are required. These exchangers can be used for highly viscous fluids at low, and medium pressures.
This post contains a detailed study of Spiral heat exchangers.
Plate-Fin Heat Exchanger
A plate-fin heat exchanger is a type of heat exchanger that uses a combination of plates and fins to transfer heat between two fluids. The heat exchanger consists of a series of parallel plates, which are separated by fins. The fins are used to increase the surface area for heat transfer and to improve the thermal efficiency of the heat exchanger.
In principle, these exchangers are similar to the plate and frame exchangers, involving alternating chambers of hot and cold fluids separated by thin metal sheets. The difference is that, two metal sheets that form one chamber are separated by wavy, perforated metallic fins which form channels to allow the passage of fluid. Two opposite sides of each chamber are sealed and the other two sides allow the inflow and outflow of fluid. The sealed sides are rotated at 90 degrees for alternating chambers. So the hot and cold fluid flows are always at 90 degrees to each other.
The fluids flow through the heat exchanger in separate channels, which are created by the plates. The fluids can flow in either the same or opposite directions, depending on the design of the heat exchanger. The plates and fins are typically made of materials such as aluminum or copper, which have high thermal conductivity.
One of the main advantages of plate-fin heat exchangers is that they have high thermal efficiency due to the large surface area provided by the fins, which increases the amount of heat that can be transferred between the fluids. The compact design of the plate-fin heat exchanger results in a low-pressure drop, which results in a relatively lower pressure drop. They are relatively lightweight and compact, and can be easily cleaned. However, they are more expensive than other types of heat exchangers such as shell and tube heat exchangers.
These exchangers can be efficiently used for a wide range of applications, wide range of temperature and pressure conditions. They are well suited for applications where high heat transfer rates are required and where the fluid flow rates are high.
Air coolers
Air coolers are used to transfer heat from a fluid to air. The fluid flows through a series of tubes, while air is forced over the tubes to transfer heat.
Air coolers utilize the ambient air for cooling the fluids which have a significantly higher temperature than ambient air (around 150C). The hot fluid flows through finned tubes across which air is blown by fans. Depending on whether the fans are located above or below the tubes, the coolers can be classified as induced draft coolers or forced draft coolers respectively. Induced draft coolers pull the flow of air across tubes. Forced draft coolers with fans located below the tubes, push the flow of air across the tubes. The cooled fluid then flows back to the process or equipment that generated the heat, while the heated air is typically released into the atmosphere.
Air cooled heat exchangers can be classified into several types such as finned tube heat exchangers, bundle type heat exchangers, compact heat exchangers and evaporative cooling heat exchnagers.
For sufficiently high heat duties it may be more economical to use cooling water instead of cooling air provided an adequate water supply is available. Air-cooled heat exchangers are commonly used in industrial and power generation applications where large amounts of heat need to be dissipated, and where the availability of cooling water is limited or costly. They are also used in air-conditioning systems, where they transfer heat from the refrigerant to the outside air.
Double Pipe Exchanger
A double-pipe heat exchanger, also known as a concentric tube heat exchanger, is a type of heat exchanger that consists of two concentric pipes, one inside the other. The inner pipe is used to carry one fluid, while the annulus, or the space between the inner and outer pipes, is used to carry the other fluid. The fluid flows either in a counter-current or co-current fashion, allowing heat transfer between them.
Usually, more corrosive fluid is pushed through the inner tube which can be equipped with scraping blades for easy cleaning. The inner heat exchanger tube can be finned on the outer surface to have an increased area for enhanced heat transfer.
Often the double pipes in these exchangers have a ‘U-tube or Hairpin structure’. The reason behind this structure is to mainly accommodate the thermal expansion of the tubes without involving expansion joints. These exchangers can be used for high pressure, high temperature and highly viscous service.
Double pipe heat exchangers are typically used in applications where the heat transfer rate is low, and the temperature difference between the two fluids is not large. They are relatively simple in design and are easy to manufacture, making them a cost-effective solution for many applications.
One of the main advantages of double-pipe heat exchangers is that they are compact and easy to install, making them well-suited for applications where space is limited. They are also relatively inexpensive to manufacture and easy to maintain. However, they are not well suited for high-pressure applications and have a relatively low heat transfer rate compared to other types of heat exchangers such as shell and tube heat exchangers.
Double pipe heat exchangers are typically made of materials such as copper, stainless steel, or aluminum, which have good thermal conductivity. This post contains a detailed study of the double-pipe heat exchanger.
Shell and Tube Exchanger
Shell and tube heat exchangers are the most widely used exchangers in a variety of industries. This has given rise to certain standards for the design of heat shell and tube exchangers. TEMA (Tubular Exchangers Manufacturers Association) standards are the most widely recognized heat exchanger design standards.
The structure of these exchangers is made of a shell side and multiple smaller tubes passing through the shell. The shell may contain baffles to induce turbulence and to increase heat transfer using the crossflow of fluids. The tubes are held together by tube sheets at both ends. There may be multiple shell-side and tube-side passes in any exchanger.
The possible flexibility in the design of shell and tube heat exchangers is mainly responsible for their wide use in a range of applications. These exchangers do not have design limitations in terms of temperature and pressure. These exchangers are easy to maintain. These exchangers can be easily designed to accommodate thermal stresses.
We can use different types of shell and tube heat exchangers depending on the application. The design of shell and tube heat exchangers involves use of various equations. This is a detailed design procedure for shell and tube heat exchangers.
Kettle Type Heat Exchanger
A kettle-type heat exchanger is a type of shell and tube heat exchanger that is shaped like a kettle or a boiling pan. It is a vertical heat exchanger where one fluid flows through the tubes and the other fluid flows over the tubes. The fluid inside the tubes is heated or cooled by the fluid outside the tubes, which acts as a heat transfer medium.
They are well-suited for heating or cooling high-viscosity fluids, as the kettle shape allows for better flow of the fluid and prevents the fluid from becoming stagnant. They are also useful for heating or cooling large volumes of fluid in a relatively small space.
Kettle-type heat exchangers can be further classified into two types, one is called a "static kettle" and the other one is called an "agitated kettle". The static kettle heat exchanger is a simple design that heats or cools the fluid inside the kettle through the fluid in the tubes. The agitated kettle heat exchanger uses an agitation system to mix the fluid inside the kettle, which increases the heat transfer rate.
Kettle-type heat exchangers are relatively efficient and easy to clean, but they can be costly to manufacture and maintain because of the kettle shape and the agitation system
Condenser
Condenser is a phase change heat exchanger, specifically used for condensing gaseous substance into liquid form by condensation / cooling process. During the condensation process latent heat is released by gaseous substance to surrounding liquid, which results in phase change from gas to liquid. This process is essential in process industries as excess heat is removed in this process, which prevents overheating. This results in improved efficiency along with improved safety of the process.
This is schematic for typical condenser used in process industries. The working of condenser is as given below.
The condenser chamber is composed of water tubes that allow for the circulation of cold water. On the other hand, the hot fluid, usually steam, enters the chamber through valves. The steam passes through the chamber and interacts with the flowing water in the tubes, resulting in the release of its latent heat and its conversion into a liquid form. Cooling water is usually circulated through the condenser to dissipate heat into the environment to maintain the proper operating temperature.
There are several types of condensers, each with its own unique design and operating characteristics. One type is the water-cooled condenser, which uses water as the cooling medium and is typically more efficient than air-cooled condensers. Another type is the air-cooled condenser, which uses air as the cooling medium and is often used in applications where water is scarce or expensive. A third type is the evaporative condenser, which removes heat from a process or system by using the evaporation of water.
Evaporator
An evaporator is also a phase change heat exchanger. Evaporator has opposite objective compared to condenser. Evaporators convert liquid into vapor state by transferring latent heat. An evaporator is also used to remove liquid from a solution by converting it into vapor.
The evaporator is a vital part of a refrigeration system that enables the transfer of heat from the surroundings to the refrigerant liquid, resulting in its conversion into a low-pressure and low-temperature vapor. The refrigerant gas is then compressed and sent to the condenser, where it is condensed back into a liquid, releasing the heat it absorbed during the evaporation process.
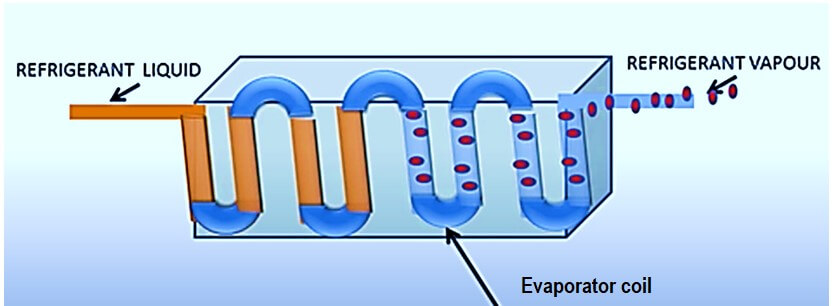
The schematic represents typical evaporator used in process industries. As the refrigerant liquid circulates through the evaporator coil, it absorbs latent heat from the surrounding environment, which causes it to undergo a phase change and convert into a low-pressure, low-temperature vapor.
There are several types of evaporators, each with its own unique design and operating characteristics. One type of evaporator is the natural circulation evaporator, which relies on gravity to circulate the liquid through the evaporator. Another type is the forced circulation evaporator, which uses a pump to circulate the liquid through the evaporator. A third type is the falling film evaporator, which features a thin film of liquid that flows down the surface of the heat transfer tubes or plates, allowing for efficient heat transfer.
Regenerative Heat Exchanger
Heat exchangers are classified into two types on the basis of construction. One is a recuperator and the other is a regenerative heat exchanger.
Regenerative heat exchangers are a type of heat exchanger that utilizes a storage medium to transfer heat between two fluid streams. The storage medium is typically a solid material, matrix, or packing with a high thermal capacity, such as ceramic, metal, or a phase change material.
The two fluid streams are alternated through the storage medium in a cyclic process, with one fluid stream passing through the medium to be heated while the other is diverted away, and then the roles are reversed. This design offers high thermal efficiency and is ideal for high-temperature applications. The choice of storage medium is crucial for optimal performance.
The twisted tube heat exchanger is a specific type of heat exchanger that employs a tube bundle design, in which the tubes are twisted in a particular pattern. The twisting generates centrifugal force, which creates vortices and turbulence within the fluid flow, thereby enhancing the convective heat transfer coefficient. This improved convective heat transfer coefficient increases the overall heat transfer rate between the fluids, resulting in a higher efficiency of heat exchanger.
Scraped Surface Heat Exchanger
The scraped surface heat exchanger is a specialized type of heat exchanger that is specifically designed to handle viscous or sticky fluids that tend to foul or build up on the heat transfer surface. The exchanger features a cylindrical shell with closely spaced, rotating, and scraping blades that prevent fouling and ensure efficient heat transfer. The heat transfer surface can be either jacketed or unjacketed.
As the fluid flows through the exchanger, the blades scrape the fluid off the surface and force it through gaps between the blades, creating turbulent flow that further enhances heat transfer. This design ensures optimal performance and efficiency in the processing of viscous fluids.
Coil Heat Exchangers
Coil heat exchangers use a coiled design for heat exchange, allowing for efficient heat transfer in a compact design. They work by circulating a hot or cold fluid through the coil, which transfers its heat to or from the surrounding environment. The heat transfer occurs through the walls of the tubes, which act as the heat exchange surface.
Coil heat exchangers offer advantages such as high efficiency, flexibility, low pressure drop, easy installation and little maintenance. The fluid flowing through the tubes can be a liquid or a gas, depending on the application.