Axial and centrifugal-type compressors typically fall into the category of rotodynamic compressors. In this post we will compare centrifugal vs axial compressors, understand the difference between them and look at different uses cases.
Term 'rotodynamic compressor' typically refers to a continuous-flow compressor, which uses rotating impellers in order to add velocity and pressure to the gas undergoing compression. Compared to positive displacement type compressors, dynamic compressors are typically smaller in size and create less vibration.
Table of content:
1. Centrifugal compressors
2. Axial Compressors
3. Centrifugal vs axial compressors
Centrifugal compressors
Centrifugal compressors typically consist of one or more stages. Each stage typically consists of an impeller (rotating element) and a diffuser (stationary element).
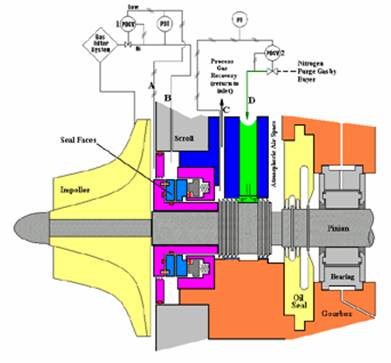
In a centrifugal compressor, the gas typically enters the impeller axially and is discharged radially. The gas hurled out radially by the rotating impeller blades. When the gas The gas then flows through the circular chamber (diffuser), following a spiral path where the velocity head of the gas gets converted to pressure head as per Bernoulli’s principle. To put it simply, the impeller imparts kinetic energy to the gas fluid, whereas the diffuser converts part of that kinetic energy into pressure head.
The extent of pressure rise in a centrifugal compressor mainly depends on the rotational speed of the impeller and the impeller size. However, the maximum allowable speed is limited by the strength of the structural material of impeller blades and sonic velocity of the gas. As a result, limitations on maximum achievable pressure rise exist. These limitations are overcome by the use of multistage centrifugal compressors, which are able to compress the gas to desirable pressure using multiple stages of centrifugal compressors operating in series.
High efficiency of the centrifugal compressors and the fact that they can be offered as packaged items at small sizes is offset by their high initial cost and the sophisticated vibration monitoring system that is usually required because of the high rotational speeds at which centrifugal compressors operate. Among others, centrifugal compressors are used in natural gas processing plants, process air applications etc.
The image shows typical impeller and diffuser at centrifugal compressor.
Check the given post for a detailed study of centrifugal compressors.
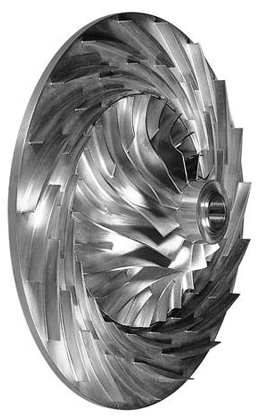
Axial Compressors
Axial flow compressors are typically used at applications with low differential pressure (head) requirements and high flow rates. A typical axial compressor consists of a drum, to which blades of specific geometry are attached.
Contrary to centrifugal compressors, axial flow compressors do not change the direction of the gas: the gas typically enters and exits the compressor in an axial direction (parallel to the axis of rotation). First, the gas is accelerated and then diffused so that its pressure is increased.
Typical applications of big-size axial compressors are those used to compress the air intake of gas turbines. These are typically multistage axial compressors, consisting of several stages. Each stage typically consists of a rotor and a stator. A rotor is a set or rotating blades, whose role is to accelerate the gas flow. A stator is a set of stationary blades whose role is to convert the velocity energy gained in the rotor to pressure energy, similar to the impeller – diffuser combination used in the centrifugal compressors.
Axial compressors have relatively high peak efficiency. On the other hand, their efficiency is good over a narrow rotational speed range. Their big weight, combined with their high starting power requirements are some of their drawbacks.
The image shows typical Axial compressor schematic.
The given post contains an overview of axial compressors including their working, advantages, disadvantages, as well as their various applications.
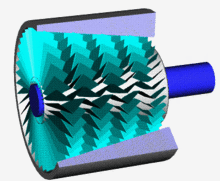
Centrifugal vs axial compressors
No | Centrifugal Compressors | Axial Compressors |
---|---|---|
1. | Centrifugal compressors use an impeller with curved blades to increase the velocity of the fluid. | Axial compressors use a series of rotating blades to increase the pressure of the fluid in a linear flow path. |
2. | Flow-through centrifugal compressors are turned perpendicular to the axis of rotation. | In axial compressors air or gas flows parallel to the axis of rotation. |
3. | Centrifugal compressors are easier to design and manufacture compared to axial compressors. | Axial compressors are complex in design compared to centrifugal compressors. |
4. | Centrifugal compressors can often create more differential pressure for efficient combustion with a single compression stage. | A single stage axial compressor is not as effective in increasing the gas pressure. Hence often multiple stages of axial compressors are used to achieve desired compression. |
5. | Centrifugal compressors can handle much less gas flow compared to the axial compressors. | Axial compressors can handle high flow rates of air or gas, making them ideal for applications that require large volumes of compressed air or gas. |
6 | The pressure loss in centrifugal compressor is high. | The pressure loss in axial compressor is low. |
7. | The centrifugal compressor is less expensive. | The axial compressor is very expensive. |