Reciprocating compressors are a type of positive displacement compressor that use a piston to compress gas or air. Reciprocating compressors are used to generate high-pressure outputs, making them essential for many industrial processes.
The purpose of this post is to provide a comprehensive overview of reciprocating compressors, including how they work, their different types and applications.
Table of content:
1. What is Reciprocating Compressor?
2. How Does a Reciprocating Compressor Operate?
3. Types of Reciprocating Compressors
3.1. Single-acting reciprocating compressor
3.2. Double-acting reciprocating compressor
4. Applications of reciprocating compressors
What is Reciprocating Compressor?
Reciprocating compressors fall into the category of positive-displacement compressors. Positive displacement compressors deal with a specific quantity of air or gas that is contained in a compression chamber. The volume of air or gas is mechanically reduced, thus increasing its pressure.
Reciprocating compressors use crankshaft-driven pistons to compress gases used in various processes. Similar to internal combustion engines, the rotary motion of the crankshaft is transformed into the linear motion of the piston. As the piston moves, it sucks in low pressure gas and increases its pressure.
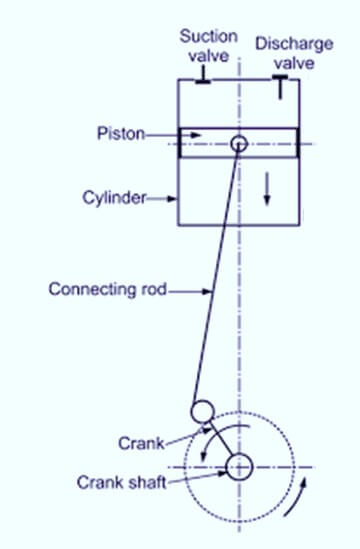
Compression cylinders, also known as stages, confine the process gas during compression. Arrangements may be of single-or dual-acting design: in the dual-acting design, compression occurs on both sides of the piston. Unlike internal combustion engines, there is no ignition involved: the gas just leaves the compressor cylinder at a high pressure than the suction pressure.
Reciprocating compressors are typically used where high compression ratio (ratio of discharge to suction pressures) is required at relevantly small flow rates, and the process fluid is relatively dry. Reciprocating compressors which are intended for higher compression ratio are designed as multistage compressors, that is with several working cylinders working in sequence.
These cylinders are driven by the same shaft, connected to a driver motor. Reciprocating compressors are typically low-speed devices and are most often direct- or belt-driven by an electric motor. Some times the motor is integral to the compressor, thus the motor shaft and compressor crankshaft are one piece, therefore eliminating the need for interconnecting coupling. At constant speed, the air flow remains almost constant with variations in discharge pressure.
How Does a Reciprocating Compressor Operate?
Reciprocating compressors operate by using a piston inside a cylinder to compress gas. The compressor's operation is similar to the engine in a car, but in reverse: instead of burning fuel to create energy, the compressor uses energy to compress gas.
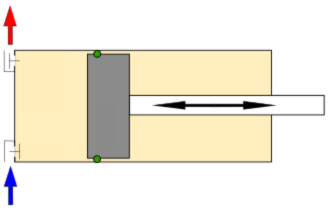
Here are the steps of the operating cycle of a reciprocating compressor:
- Suction: The compressor's intake valve opens, and the piston moves downward, creating a low-pressure area inside the cylinder. Gas from the outside then flows into the cylinder.
- Compression: The piston moves back up, compressing the gas into a smaller volume and increasing its pressure. This compressed gas is then trapped in the cylinder.
- Discharge: The discharge valve opens, and the compressed gas flows out of the cylinder and into the system it is connected to.
- Re-expansion: After the gas is discharged, the piston moves back down again, opening the intake valve and allowing the low-pressure gas from the outside to enter the cylinder again. This process repeats continuously to maintain the pressure and flow of gas in the system.
A reciprocating compressor be damaged when the discharge service valve is closed.
Types of Reciprocating Compressors
Single-acting reciprocating compressor
In a single-acting reciprocating compressor, the gas is compressed only during the upward stroke of the piston. During the downward stroke, the gas is discharged but not compressed. This type of compressor is simple in design, has low initial cost, and is suitable for low flow rate and low-pressure applications. However, it has lower efficiency compared to double-acting compressors.
Double-acting reciprocating compressor
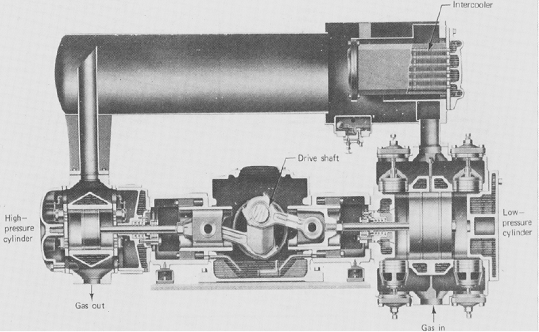
In a double-acting reciprocating compressor, gas is compressed during both the upward and downward strokes of the piston. This type of compressor is more efficient than the single-acting type and is suitable for high flow rate and high-pressure applications. Double-acting compressors are often larger in size and more expensive than single-acting compressors.
In both types of reciprocating compressors, the piston is driven by a crankshaft, which is powered by an electric motor, engine, or turbine. The compressors can also have multiple stages to achieve higher compression ratios. In a multi-stage compressor, the gas is compressed in two or more stages, with each stage having its cylinder and piston. This allows the compressor to achieve higher compression ratios without overheating or damaging the compressor components.
Applications of reciprocating compressors
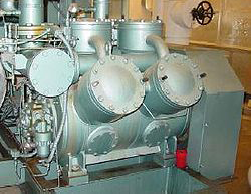
Reciprocating compressors are used to compress natural gas (gas transmission pipeline applications), supply high-pressure gas for oil well drilling for gas lift, as well as in various industrial or chemical applications involving air and refrigerant compression, e.g. in refrigeration plants.