Table of content:
1. Types of Pumps
1.1. Positive Displacement Pumps
1.2. Centrifugal Pumps
1.3. Vacuum Pumps
1.4. Canned Pumps
2. Pump Operations
3. Pump Sizing Calculations
4. Testing of Pumps
5. Pump Installation
6. P&ID Symbol of Pumps
7. API standards for pump design, operation and maintenance
8. Selection of pump
Types of Pumps
Pumps can be broadly classified into two basic categories: Centrifugal pumps and Positive Displacement pumps. Depending on the fluid service, the flowrate handled and differential pressure requirements, either of the pump types can be used effectively.
Positive Displacement Pumps
Positive displacement pumps are a type of pump that moves fluid by trapping a fixed amount of it in a cavity and then forcing it through the pump and into the discharge piping. These pumps use a reciprocating, rotary, or diaphragm mechanism to move the fluid.
- Reciprocating pumps, also known as piston pumps, use a piston to draw fluid into a chamber and then push it out through a discharge valve.
- Rotary pumps, on the other hand, use a rotating mechanism such as gears, lobes, or screws to trap and move the fluid through the pump.
- Diaphragm pumps use a flexible diaphragm that moves back and forth to create a pulsating flow of fluid.
For positive displacement pumps, the discharge flowrate is nearly independent of the downstream pressure. Positive displacement pumps have different types as indicated in the following figures.
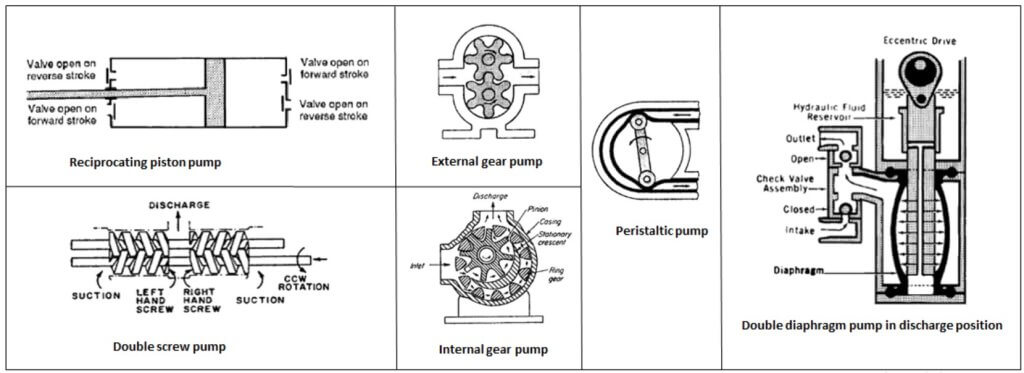
Centrifugal Pumps
Centrifugal pumps have rotating equipment parts imparting momentum to the fluid particles which is later converted to pressure. For centrifugal pumps the discharge flowrate and differential head developed in the pumps are strongly dependent on each other.
The figure gives an idea of the basic structure of a centrifugal pump. Check the given post for in-depth explanation of centrifugal pumps, including priming, cavitation, P&ID arrangement and typical datasheet.
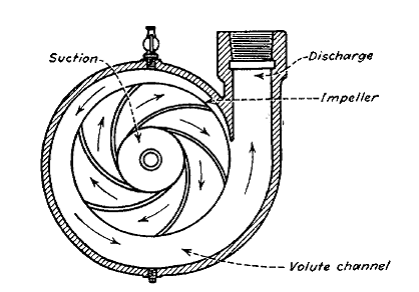
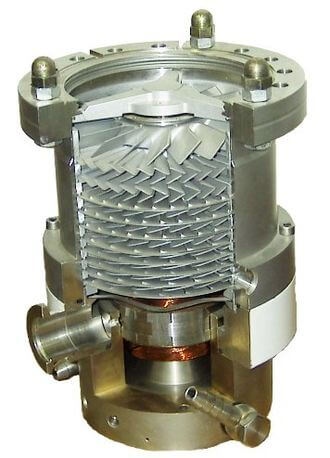
Vacuum Pumps
A vacuum pump is a device that removes gas molecules from a sealed volume to create a partial or near-total vacuum. The purpose of a vacuum pump is to reduce the pressure inside a closed system to create a vacuum, which has a wide range of industrial, scientific, and medical applications.
Study everything about vacuum pumps in this post including its types, parts and uses.
Canned Pumps
A canned pump is a type of centrifugal pump that features a unique construction where the motor and impeller are enclosed in a metal can. The can separates the pumped fluid from the motor, which prevents the fluid from coming into contact with the motor and causing damage.
Study everything about canned pumps in this post.
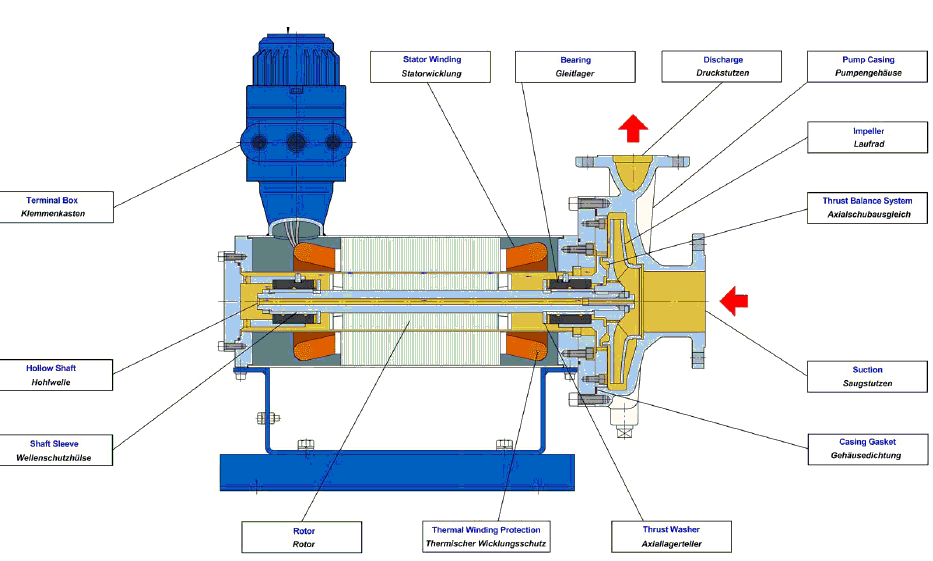
Pump Operations
Pump operations refer to the procedures and activities involved in operating a pump, which is a device used to transfer fluids or gases from one location to another. Pump operations can include the start-up procedure, monitoring, maintenance, shutdown procedures and troubleshooting. Effective pump operations require careful attention to all these points.
Pump Priming
Cavitation in pumps
Pump Overloading
Pump Recirculation
Vibration in pumps
Troubleshooting for pumps
Pump Maintenance
Pump Performance Test
Reliability coefficient for pumps
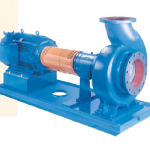
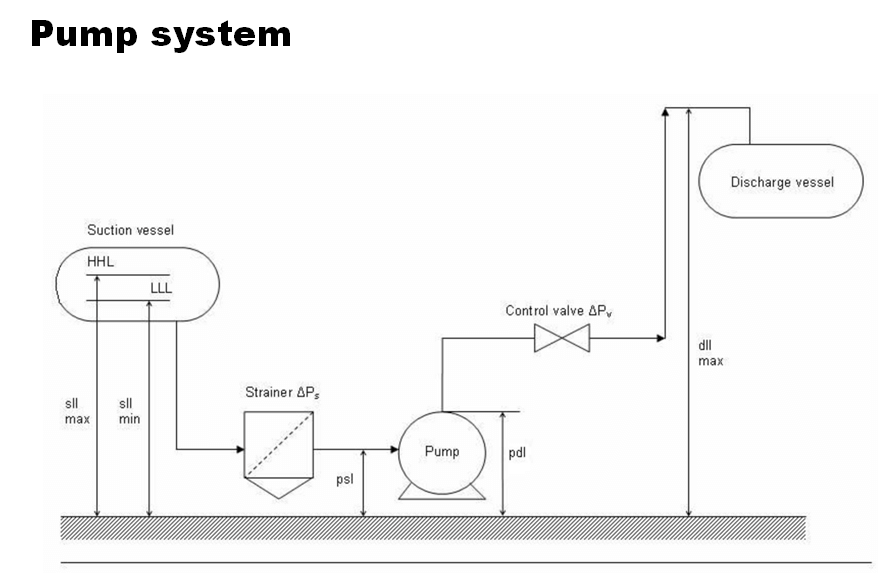
Pump Sizing Calculations
Pump sizing calculations are a critical aspect of designing any fluid handling system. Correctly sizing a pump is essential to ensure that the system operates efficiently and effectively, with minimal energy consumption and maintenance requirements. Check this post to explore the basics of pump sizing calculations and guide you through the essential steps required to determine the flow rate, NPSH, head, and power requirements for a pump.
NPSH calculation
Pump Performance curves
Pump Specific Speed and Pump Suction Specific Speed
Pump power calculation
Pump affinity laws
Testing of Pumps
Pumps are a critical component of many industrial processes. Their proper functioning is essential for the efficient and safe operation of many industries. However, pumps can experience issues that can reduce their performance, reliability, and safety. To ensure the proper functioning of pumps, it is crucial to test them regularly. In this post, we will discuss methods for the testing of pumps, their importance, and how they help ensure efficient and safe pump operation.
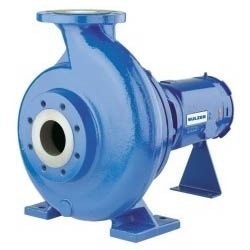
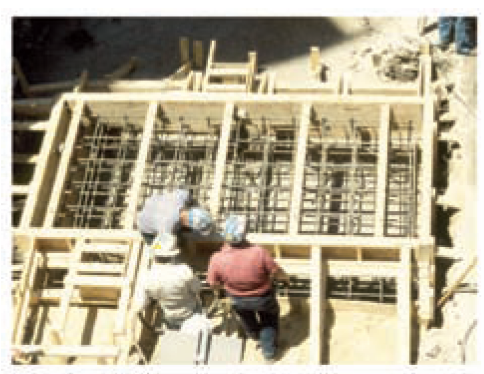
Pump Installation
Proper pump installation is crucial for ensuring reliable and efficient operation of a pumping system. A poorly installed pump can lead to costly repairs, downtime, and even safety hazards.
In this post, the planning process for pump installation and the steps involved in installing and commissioning a pump has been discussed. By following the guidelines and best practices outlined in this post, you can ensure that your pump is installed correctly and operates efficiently.
P&ID Symbol of Pumps
It is important to know pumps P&ID symbols to read P&ID diagrams. Symbols of different types of pump are given here.
Also check post on typical representation of P&ID or Piping & Instrumentation Diagram of a pump.
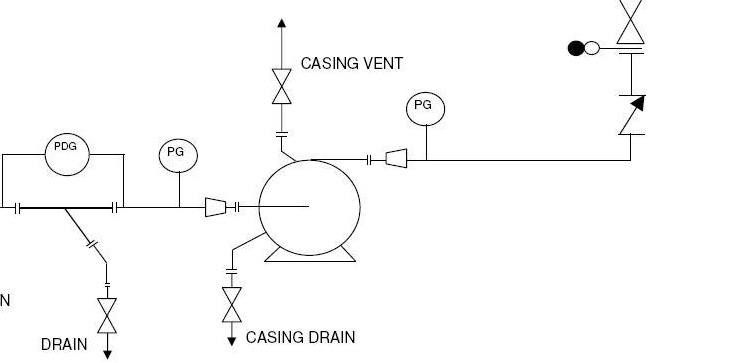
API standards for pump design, operation and maintenance
Check this post for the list of pump design standards from organizations like - API, ANSI, ASME etc. as well as standards for maintenance and operations of different kinds of pumps.
Selection of pump
When it comes to selecting between centrifugal pumps and positive displacement pumps a number of factors have to be taken into consideration.
1. Fluid service handled: Centrifugal pumps are preferred for a wide range of fluids from clean and clear non-abrasive fluids to abrasive fluids with high solid content. But centrifugal pumps run into limitations when it comes to handling highly viscous fluids and they have very low tolerance for handling entrained gases. Positive displacement pumps (reciprocating and rotary type) are preferred for handling highly viscous fluids and fluids with entrained gases. I general, it can be stated that positive displacement pumps are equipped to handle a wider range of fluids.
2. Flowrates handled: Centrifugal pumps are preferred for handling of higher flowrates. But centrifugal pumps have limitations on handling of lower flowrates. Positive displacement pumps are preferred when it comes to low flowrates.
3. Differential pressure head: A single stage centrifugal pump cannot deliver very high discharge pressure unless it is operated at very high speeds, which can turn out to be expensive. The operation of a positive displacement pump is nearly independent of the discharge pressure encountered downstream. Positive displacement can achieve very high differential pressures and hence they are preferred for such applications.
4. Efficiency: A Centrifugal pump can operate at the best efficiency for a narrow range of flowrate and differential head values. The positive displacement pumps are not limited in such ways.
5. Space constraints: Centrifugal pumps are compact and require less space compared to reciprocating pumps handling similar flowrates. In case of positive displacement pumps, rotary type of pumps should be preferred to reciprocating pumps as rotary pumps take up less space.
6. Pulsating flow: Centrifugal pumps deliver a smooth flow. Reciprocating pumps deliver a pulsating flow profile thus requiring a pulsation dampener at the pump discharge. Rotary pumps are preferred to reciprocating pumps as they can deliver a smooth flow as well.
7. Costs: Centrifugal pumps are most widely used and regarded as economical. They have low initial cost, low maintenance cost but high power cost. Out of positive displacement pumps, reciprocating pumps are the most expensive alternatives. Reciprocating pumps high initial and maintenance cost, but they consume lower power. Rotary type of positive displacement pumps are always an attractive alternative even to the centrifugal pumps. Rotary pumps have low initial, maintenance and power costs.
8. Summary: Centrifugal pumps have been found suitable for the widest range of application and are most widely used. A variety of users prefer to use centrifugal pumps because of their familiarity with these pumps. The comparison done here indicates that often times positive displacement pumps, especially the rotary type pumps can prove to be an attractive alternative to centrifugal pumps. Use of positive displacement pumps should be specially considered for cases with low flows, entrained gases, highly viscous fluid, high differential head.